Как получают и из чего делают железо (сталь)?
Железо и стали на его основе используются повсеместно в промышленности и обыденной жизни человека. Однако мало кто знает, из чего делают железо, вернее, как его добывают и преобразовывают в сплав стали.
Популярное заблуждение
Для начала определимся с понятиями, поскольку люди часто путаются и не совсем понимают, что такое железо вообще. Это химический элемент и простое вещество, которое в чистом виде не встречается и не используется. А вот сталь – это сплав на основе железа. Она богата на различные химические элементы, а также содержит углерод в своем составе, который необходим для придания прочности и твердости.
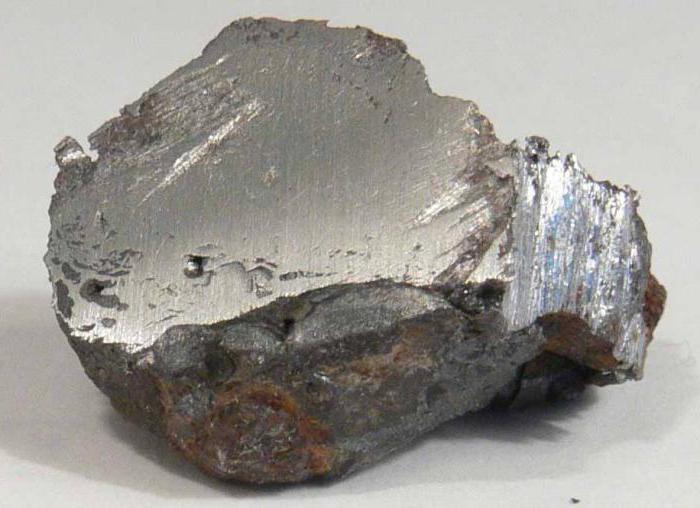
Следовательно, не совсем правильно рассуждать о том, из чего делают железо, так как оно представляет собой химический элемент, который есть в природе. Человек из него делает сталь, которая в дальнейшем может использоваться для изготовления чего-либо: подшипников, кузовов автомобилей, дверей и т. д. Невозможно перечислить все предметы, которые из нее производятся. Итак, ниже мы не будем разбирать, из чего делают железо. Вместо этого поговорим о преобразовании этого элемента в сталь.
Добыча
В России и мире существует множество карьеров, где добывают железную руду. Это огромные и тяжелые камни, которые достаточно сложно достать из карьера, так как они являются частью одной большой горной породы. Непосредственно на карьерах в горную породу закладывают взрывчатку и взрывают ее, после чего огромные куски камней разлетаются в разные стороны. Затем их собирают, грузят на большие самосвалы (типа БелАЗ) и везут на перерабатывающий завод. Из этой горной породы и будет добываться железо.
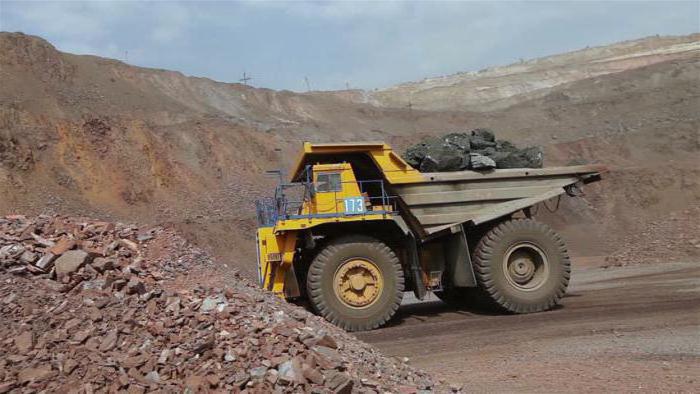
Иногда, если руда находится на поверхности, то ее вовсе необязательно подрывать. Ее достаточно расколоть на куски любым другим способом, погрузить на самосвал и увезти.
Производство
Итак, теперь мы понимаем, из чего делают железо. Горная порода является сырьем для его добычи. Ее отвозят на перерабатывающее предприятие, загружают в доменную печь и нагревают до температуры 1400-1500 градусов. Эта температура должна держаться в течение определенного времени. Содержащееся в составе горной породы железо плавится и приобретает жидкую форму. Затем его остается разлить в специальные формы. Образовавшиеся шлаки при этом отделяют, а само железо получается чистым. Затем агломерат подают в бункерные чаши, где он продувается потоком воздуха и охлаждается водой.
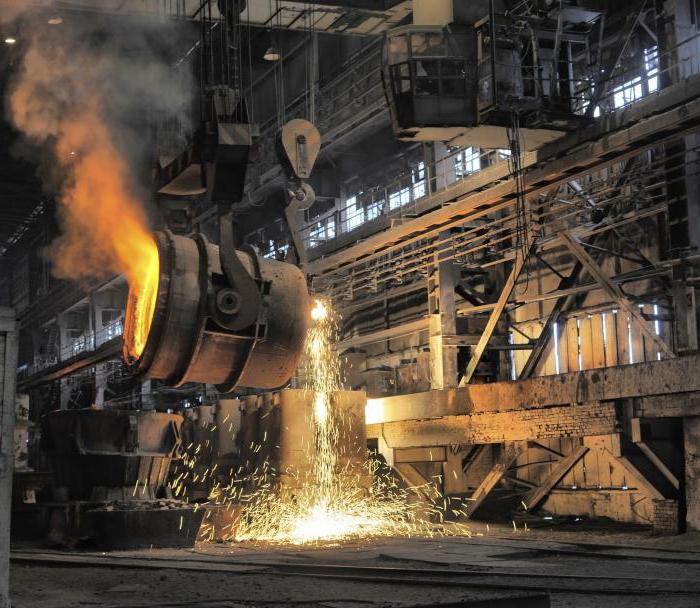
Есть и другой способ получения железа: горную породу дробят и подают на специальный магнитный сепаратор. Так как железо имеет способность намагничиваться, то минералы остаются на сепараторе, а вся пустая порода вымывается. Конечно, чтобы железо превратить в металл и придать ему твердую форму, его необходимо легировать с помощью другого компонента – углерода. Его доля в составе очень мала, однако именно благодаря нему металл становится высокопрочным.
Стоит отметить, что в зависимости от объема добавляемого в состав углерода сталь может получаться разной. В частности, она может быть более или менее мягкой. Есть, например, специальная машиностроительная сталь, при изготовлении которой к железу добавляют всего 0,75 % углерода и марганец.
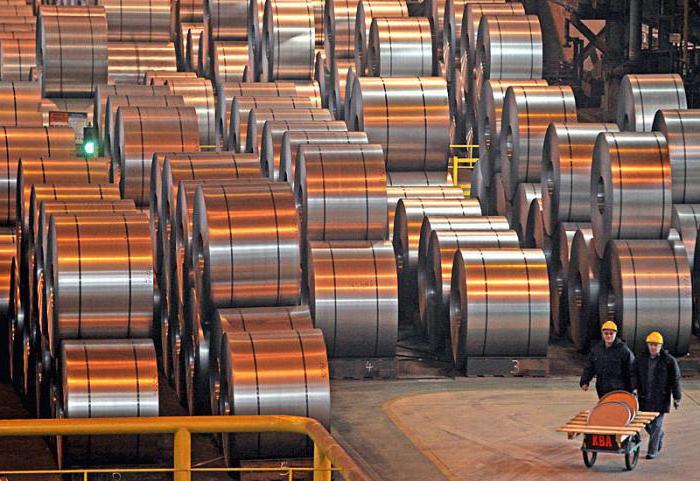
Теперь вы знаете, из чего делают железо и как его преобразовывают в сталь. Конечно, способы описаны весьма поверхностно, но суть они передают. Нужно запомнить, что из горной породы делают железо, из чего далее могут получать сталь.
Производители
На сегодняшний день в разных странах есть крупные месторождения железной руды, которые являются базой для производства мировых запасов стали. В частности, на Россию и Бразилию приходится 18 % мирового производства стали, на Австралию – 14 %, Украину – 11 %. Самыми крупными экспортерами является Индия, Бразилия, Австралия. Отметим, что цены на металл постоянно меняются. Так, в 2011 году стоимость одной тонны металла составляла 180 долларов США, а к 2016 году была зафиксирована цена в 35 долларов США за тонну.
Заключение
Теперь вы знаете, из чего состоит железо (имеется в виду металл) и как его производят. Применение этого материала распространено во всем мире, и его значение практически невозможно переоценить, так как используется он в промышленных и бытовых отраслях. К тому же экономика некоторых стран построена на базе изготовления металла и его последующего экспорта.
Мы рассмотрели, из чего состоит сплав. Железо в его составе смешивается с углеродом, и подобная смесь является основной для изготовления большинства известных металлов.
Железо — общая характеристика элемента, химические свойства железа и его соединений
Желе́зо — элемент побочной подгруппы восьмой группы четвёртого периода периодической системы химических элементов Д. И. Менделеева с атомным номером 26. Обозначается символом Fe (лат. Ferrum). Один из самых распространённых в земной коре металлов (второе место после алюминия). Металл средней активности, восстановитель.
Основные степени окисления — +2, +3
Простое вещество железо — ковкий металл серебристо-белого цвета с высокой химической реакционной способностью: железо быстро корродирует при высоких температурах или при высокой влажности на воздухе. В чистом кислороде железо горит, а в мелкодисперсном состоянии самовозгорается и на воздухе.
Химические свойства простого вещества — железа:
Ржавление и горение в кислороде
1) На воздухе железо легко окисляется в присутствии влаги (ржавление):
4Fe + 3O2 + 6H2 O → 4Fe(OH)3
Накалённая железная проволока горит в кислороде, образуя окалину — оксид железа (II, III):
3Fe + 2O2
3Fe+2O2→(Fe IIFe2III)O4 (160 °С)
2) При высокой температуре (700–900°C) железо реагирует с парами воды:
3Fe + 4H2O –t°→ Fe3O4 + 4H2
3) Железо реагирует с неметаллами при нагревании:
2Fe+3Cl2→2FeCl3 (200 °С)
2Fe + 3Br2 –t°→ 2FeBr3
Fe + S –t°→ FeS (600 °С)
Fe+2S → Fe+2(S2-1) (700°С)
4) В ряду напряжений стоит левее водорода, реагирует с разбавленными кислотами НСl и Н2SO4, при этом образуются соли железа(II) и выделяется водород:
Fe + 2HCl → FeCl2 + H2 (реакции проводятся без доступа воздуха, иначе Fe+2 постепенно переводится кислородом в Fe+3 )
Fe + H2SO 4(разб.) → FeSO4 + H2
В концентрированных кислотах–окислителях железо растворяется только при нагревании, оно сразу переходит в катион Fе3+:
2Fe + 6H2SO4(конц.) –t°→ Fe2(SO4)3 + 3SO2 + 6H2O
Fe + 6HNO3(конц.) –t°→ Fe(NO3)3 + 3NO2 + 3H2O
(на холоде концентрированные азотная и серная кислоты пассивируют железо).
Железный гвоздь, погруженный в голубоватый раствор медного купороса, постепенно покрывается налетом красной металлической меди
5) Железо вытесняет металлы, стоящие правее его в ряду напряжений из растворов их солей.
Fe + CuSO4 → FeSO4 + Cu
6)
Амфотерность железа проявляется только в концентрированных щелочах при кипячении:
Fе + 2NaОН (50 %) + 2Н2O= Nа
и образуется осадок тетрагидроксоферрата(II) натрия.
Техническое железо — сплавы железа с углеродом: чугун содержит 2,06-6,67 % С, сталь 0,02-2,06 % С, часто присутствуют другие естественные примеси (S, Р, Si) и вводимые искусственно специальные добавки (Мn, Ni, Сr), что придает сплавам железа технически полезные свойства — твердость, термическую и коррозионную стойкость, ковкость и др.
Доменный процесс производства чугуна
Доменный процесс производства чугуна составляют следующие стадии:
а) подготовка (обжиг) сульфидных и карбонатных руд — перевод в оксидную руду:
FeS2→Fe2O3 (O2,800°С, -SO2) FeCO3→Fe2O3 (O2,500-600°С, -CO2)
б) сжигание кокса при горячем дутье:
С(кокс) + O2 (воздух) →СO2 (600—700°С) СO2 + С(кокс)
⇌ 2СО (700—1000 °С)в) восстановление оксидной руды угарным газом СО последовательно:
Fe2O3→(CO) (FeIIFe2III)O4→(CO) FeO→(CO) Fe
г) науглероживание железа (до 6,67 % С) и расплавление чугуна:
Fе(т)→(C(кокс) 900—1200°С)Fе(ж) (чугун, t пл 1145°С)
В чугуне всегда в виде зерен присутствуют цементит Fe2С и графит.
Производство стали
Передел чугуна в сталь проводится в специальных печах (конвертерных, мартеновских, электрических), отличающихся способом обогрева; температура процесса 1700-2000 °С. Продувание воздуха, обогащенного кислородом, приводит к выгоранию из чугуна избыточного углерода, а также серы, фосфора и кремния в виде оксидов. При этом оксиды либо улавливаются в виде отходящих газов (СО2, SО2), либо связываются в легко отделяемый шлак — смесь Са
Получение чистого железа в промышленности — электролиз раствора солей железа, например:
FеСl2→ Fе↓ + Сl2↑ (90°С) (электролиз)
(существуют и другие специальные методы, в том числе восстановление оксидов железа водородом).
Чистое железо применяется в производстве специальных сплавов, при изготовлении сердечников электромагнитов и трансформаторов, чугун — в производстве литья и стали, сталь — как конструкционный и инструментальный материалы, в том числе износо-, жаро- и коррозионно-стойкие.
Оксид железа(II) FеО. Амфотерный оксид с большим преобладанием основных свойств. Черный, имеет ионное строение Fе2+ O2-. При нагревании вначале разлагается, затем образуется вновь. Не образуется при сгорании железа на воздухе. Не реагирует с водой. Разлагается кислотами, сплавляется со щелочами. Медленно окисляется во влажном воздухе. Восстанавливается водородом, коксом. Участвует в доменном процессе выплавки чугуна. Применяется как компонент керамики и минеральных красок. Уравнения важнейших реакций:
4FеО ⇌(FeIIFe2 III) + Fе (560—700 °С , 900—1000°С)
FеО + 2НС1 (разб.) = FеС12 + Н2O
FеО + 4НNO3 (конц.) = Fе(NO3)3 +NO2↑ + 2Н2O
FеО + 4NаОН =2Н2O + Nа4FеO3(красн.) триоксоферрат(II) (400—500 °С)
FеО + Н2 =Н2O + Fе (особо чистое) (350°С)
FеО + С(кокс) = Fе + СО (выше 1000 °С)
FеО + СО = Fе + СO2 (900°С)
4FеО + 2Н2O(влага) + O2(воздух)
6FеО + O2 = 2(FeIIFe2III )O4 (300—500°С)
Получение в лаборатории: термическое разложение соединений железа (II) без доступа воздуха:
Fе(ОН)2 = FеО + Н2O (150-200 °С)
FеСОз = FеО + СO2 (490-550 °С)
Оксид дижелеза (III) – железа(II) (FeIIFe2III )O4 . Двойной оксид. Черный, имеет ионное строение Fe2+(Fе3+)2(O2-)4. Термически устойчив до высоких температур. Не реагирует с водой. Разлагается кислотами. Восстанавливается водородом, раскаленным железом. Участвует в доменном процессе производства чугуна. Применяется как компонент минеральных красок (железный сурик), керамики, цветного цемента. Продукт специального окисления поверхности стальных изделий (чернение, воронение
). По составу отвечает коричневой ржавчине и темной окалине на железе. Применение брутто-формулы Fe3O4 не рекомендуется. Уравнения важнейших реакций:2(FeIIFe2 III )O4 = 6FеО + O2 (выше 1538 °С)
(FeIIFe2III )O4 + 8НС1 (разб.) = FеС12 + 2FеС13 + 4Н2O
(FeIIFe2III )O4 +10НNO3 (конц.) =3Fе(NO3)3 + NO2↑+ 5Н2O
(FeIIFe2III )O4 + O2 (воздух) = 6Fе2O3 (450-600°С)
(FeIIFe2III )O4 + 4Н2 = 4Н2O + 3Fе (особо чистое, 1000 °С)
(FeIIFe2III )O4 + СО =ЗFеО + СO2 (500—800°C)
Получение: сгорание железа (см.) на воздухе.
В природе — оксидная руда железа магнетит.
Оксид железа(III) Fе2О3. Амфотерный оксид с преобладанием основных свойств. Красно-коричневый, имеет ионное строение (Fе 3+)2(O2-)3. Термически устойчив до высоких температур. Не образуется при сгорании железа на воздухе. Не реагирует с водой, из раствора выпадает бурый аморфный гидрат Fе2O3 nН2О. Медленно реагирует с кислотами и щелочами. Восстанавливается монооксидом углерода, расплавленным железом. Сплавляется с оксидами других металлов и образует двойные оксиды — шпинели (технические продукты называются ферритами). Применяется как сырье при выплавке чугуна в доменном процессе, катализатор в производстве аммиака, компонент керамики, цветных цементов и минеральных красок, при термитной сварке стальных конструкций, как носитель звука и изображения на магнитных лентах, как полирующее средство для стали и стекла.
Уравнения важнейших реакций:
6Fе2O3 = 4(FeIIFe2III )O4 +O2 (1200—1300 °С)
Fе2O3 + 6НС1 (разб.) →2FеС13 + ЗН2O (t) (600°С,р)
Fе2O3 + 2NaОН (конц.) →Н2O+ 2NаFеO2 (красн.) диоксоферрат(III)
Fе2О3 + МО=(МIIFе2III)O4 (М=Сu, Мn, Fе, Ni, Zn)
Fе2O3 + ЗН2 =ЗН2O+ 2Fе (особо чистое, 1050—1100 °С)
Fе2O3 + Fе = ЗFеО (900 °С)
3Fе2O
Получение в лаборатории — термическое разложение солей железа (III) на воздухе:
Fе2(SO4)3 = Fе2O3 + 3SO3 (500-700 °С)
4{Fе(NO3)3 9 Н2O} = 2FеaO3 + 12NO2+ 3O2 + 36Н2O (600-700 °С)
В природе — оксидные руды железа гематит Fе2O3 и лимонит Fе2O3 nН2O
Гидроксид железа (II) Fе(ОН)2. Амфотерный гидроксид с преобладанием основных свойств. Белый (иногда с зеленоватым оттенком), связи Fе — ОН преимущественно ковалентные. Термически неустойчив. Легко окисляется на воздухе, особенно во влажном состоянии (темнеет). Нерастворим в воде. Реагирует с разбавленными кислотами, концентрированными щелочами. Типичный восстановитель. Промежуточный продукт при ржавлении железа. Применяется в изготовлении активной массы железоникелевых аккумуляторов.
Уравнения важнейших реакций:
Fе(OН)2 = FеО + Н2O (150-200 °С, в атм.N2)
Fе(ОН)2 + 2НС1 (разб.) =FеС12 + 2Н2O
Fе(ОН)2 + 2NаОН (> 50%) = Nа2[Fе(ОН)4] ↓(сине-зеленый) (кипячение)
4Fе(ОН)2 (суспензия) + O2 (воздух) →4FеО(ОН)↓ + 2Н2O (t)
2Fе(ОН)2 (суспензия) +Н2O2 (разб.) = 2FеО(ОН)↓ + 2Н2O
Fе(ОН)2 + КNO3(конц.) = FеО(ОН)↓ + NO↑+ КОН (60 °С)
Получение: осаждение из раствора щелочами или гидратом аммиака в инертной атмосфере:
Fе2+ + 2OH (разб.) = Fе(ОН)2↓
Fе2+ + 2(NH3Н2O) = Fе(ОН)2↓+ 2NH4
Метагидроксид железа FеО(ОН). Амфотерный гидроксид с преобладанием основных свойств. Светло-коричневый, связи Fе — О и Fе — ОН преимущественно ковалентные. При нагревании разлагается без плавления. Нерастворим в воде. Осаждается из раствора в виде бурого аморфного полигидрата Fе2O3 nН2O, который при выдерживании под разбавленным щелочным раствором или при высушивании переходит в FеО(ОН). Реагирует с кислотами, твердыми щелочами. Слабый окислитель и восстановитель. Спекается с Fе(ОН)2. Промежуточный продукт при ржавлении железа. Применяется как основа желтых минеральных красок и эмалей, поглотитель отходящих газов, катализатор в органическом синтезе.
Соединение состава Fе(ОН)3 не известно (не получено).
Уравнения важнейших реакций:
Fе2O3. nН2O→(200-250 °С, —H2O) FеО(ОН)→( 560-700° С на воздухе , -h3O) →Fе2О3
FеО(ОН) + ЗНС1 (разб.) =FеС13 + 2Н2O
FeO(OH)→Fe2O3.nH2O -коллоид (NаОН (конц.))
FеО(ОН)→Nа3[Fе(ОН)6] белый , Nа5[Fе(OН)8желтоватый (75 °С, NаОН( т))
2FеО(ОН) + Fе(ОН)2=( FeIIFe2III )O4 + 2Н2O (600—1000 °С)
2FеО(ОН) + ЗН2 = 4Н2O+ 2Fе (особо чистое, 500—600 °С)
2FеО(ОН) + ЗВr2 + 10КОН = 2К2FеO4 + 6Н2O + 6КВr
Получение: осаждение из раствора солей железа(Ш) гидрата Fе2О3 nН2O и его частичное обезвоживание (см. выше).
В природе — оксидная руда железа лимонит Fе2O3 nН2О и минерал гётит FеО(ОН).
Феррат калия К2FеО4. Оксосоль. Красно-фиолетовый, разлагается при сильном нагревании. Хорошо растворим в концентрированном растворе КОН, реагирует с кипящей водой, неустойчив в кислотной среде. Сильный окислитель.
Качественная реакция — образование красного осадка феррата бария. Применяется в синтезе ферритов — промышленно важных двойных оксидов железа (III) и других металлов.
Уравнения важнейших реакций:
4К2FеO4= 4КFеO2 + 3O2 + 2К2O (700 °С)
4К2FеO4 + 6Н2O (гор.) =4FeО(ОН)↓ + 8КОН + 3O2↑
FеО42- + 2OН+(разб.) =4Fе3+ + 3O2↑+10Н2O
FеО42- + 2(NH3. Н2O) →2FеО(ОН)↓ + N2↑+ 2Н2O+ 4OН—
FеО42- + Ва2+ = ВаFеO4 (красн.)↓ (в конц. КОН)
Получение: образуется при окислении соединений железа, например метагидроксида FеО(ОН), бромной водой, а также при действии сильных окислителей (при спекании) на железо
Fе + 2КОН + 2КNO3 = К2FеO4 + 3КNO2+ H2O (420 °С)
и электролизе в растворе:
электролиз
Fе + 2КОН (конц.) + 2Н2O→ЗН2↑ + К2FеO4 ( электролиз)
(феррат калия образуется на аноде).
Качественные реакции на ионы Fе2+ и Fе3+
Обнаружение ионов Fе2+ и Fе3+в водном растворе проводят с помощью реактивов К3[Fе(СN)6] и К4[Fе(СN)6] соответственно; в обоих случаях выпадает синий продукт одинакового состава и строения, КFеIII[FеII (СN)6]. В лаборатории этот осадок называют берлинская лазурь, или турнбуллева синь:
Fе2+ + К+ + [Fе(СN)6]3- = КFеIII[FеII (СN) 6]↓
Fе3+ + К+ + [Fе(СN)6]4- = КFеIII[FеII (СN) 6]↓
Химические названия исходных реактивов и продукта реакций:
К3FеIII[Fе(СN) 6]- гексацианоферрат (III) калия
К4FеIII[Fе (СN) 6]- гексацианоферрат (II) калия
КFеIII[FеII (СN) 6]- гексацианоферрат (II) железа (Ш) калия
Кроме того, хорошим реактивом на ионы Fе3+ является тиоцианат-ион NСS—, железо (III) соединяется с ним, и появляется ярко-красная («кровавая») окраска:
Fе3+ + 6NСS— = [Fе(NСS)6]3-
Этим реактивом (например, в виде соли КNСS) можно обнаружить даже следы железа (III) в водопроводной воде, если она проходит через железные трубы, покрытые изнутри ржавчиной.
История производства и использования железа — Википедия
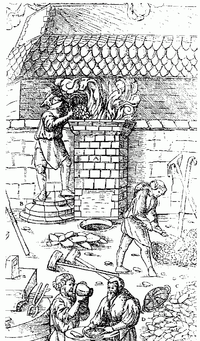
История производства и использования железа берёт своё начало в доисторической эпохе, скорее всего, с использования метеоритного железа. Выплавка в сыродутной печи применялась в XII веке до н. э. в Индии, Анатолии и на Кавказе. Также отмечается использование железа при выплавке и изготовлении орудий и инструментов в 1200 году до н. э. в Африке южнее Сахары[2][3]. Уже в первом тысячелетии до н. э. использовалось кованое железо (англ. Wrought iron). Об обработке железа упоминается в первой книге Библии (Быт. 4:22).
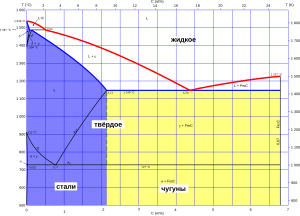
Материал, в обиходе называемый «железом», как правило, является сталью или чугуном и представляет собой сплав железа (Fe), как химического элемента, с углеродом (C). Кроме железа и углерода сплав содержит незначительные количества других химических элементов.
При концентрации углерода в сплаве менее 0,3 % получается мягкий пластичный тугоплавкий (температура плавления железа 1539 °C) сплав, за которым и закрепляется название его основного ингредиента — железа. Представление о том железе, с которым имели дело наши предки, сейчас можно получить, исследовав механические свойства гвоздя.
При концентрации углерода в сплаве от 0,3 до 2,14 % сплав называется «сталью». В первозданном виде сталь походит по своим свойствам на железо, но, в отличие от него, поддается закалке: при резком охлаждении после нагрева до определённых температур сталь приобретает большую твёрдость — замечательное достоинство, однако, почти совершенно сводимое на нет приобретённой в процессе той же закалки хрупкостью.
При концентрации углерода в сплаве свыше 2,14 % сплав называется «чугуном». Чугун — хрупкий легкоплавкий сплав, пригодный для литья, но не поддающийся обработке ковкой. Чугун насыщен графитовыми включениями, делающими его неоднородным и механически непрочным. Температура плавления чугуна варьируется от 1150 до 1300 °C.
Технологии производства и обработки железа и сплавов[править | править код]
Для производства железа исторически применялось несколько технологий, которые сложно расположить в хронологическом порядке.
Метеоритное железо[править | править код]
Использование железа началось намного раньше, чем его производство. Иногда люди находили куски серовато-чёрного металла, попавшие на Землю с метеоритами — метеоритное железо, использовали их для изготовления оружия: перековывали в кинжалы или наконечники копий. Метеоритное железо было более прочным и пластичным, чем бронза, и дольше «держало» остроту лезвия. Поскольку железные метеориты содержали железоникелевый сплав, можно предположить, что качество некоторых уникальных кинжалов могло соперничать с современным ширпотребом[4]. Однако, та же уникальность приводила к тому, что такое оружие оказывалось не на поле боя, а в сокровищнице очередного правителя.
Сыродутная печь[править | править код]
Первым устройством для получения железа из руды стала одноразовая сыродутная печь (сыродутный горн, домница). Несмотря на наличие недостатков способ получения железа с использованием такой печи долгое время оставался единственным способом получения железа из руды. На Руси появление первых домниц относят к IX веку[5].
Впервые железо научились обрабатывать народы Анатолии. Древние греки считали, что открывателями железа был народ халибов. В литературе этот народ назывался устойчивым выражением «отец железа». Слово «сталь» на греческом языке («Χάλυβς») происходит от этого этнонима.
«Железная революция» началась на рубеже I тысячелетия до нашей эры в Ассирии. Железные мечи научились изготавливать представители Гальштатской культуры. С VIII века до нашей эры сварочное железо быстро стало распространяться в Европе, в III веке до нашей эры оно вытеснило бронзу в Галлии, во II веке новой эры появилось в Германии, а в VI веке уже широко употреблялось в Скандинавии; племенами же, проживающими на территории будущей Руси — киммерийцами, а позже скифами и сарматами — железо использовалось ещё до н. э.. В Японии железный век наступил только в VII веке нашей эры.
Известный популяризатор науки Айзек Азимов так описывает историю перехода человечества из бронзового века в железный[6]:
![]() | Где-то около XV—XIV вв. до н. э. техника выплавки и науглероживания железа была разработана в кавказских предгорьях в Урарту. Эта страна находилась тогда под властью Хеттского царства, которое находилось на высшей точке своей мощи. Хеттские цари тщательно охраняли монополию на новую технику, ибо понимали её важность. Вначале получали только маленькие партии железа, и в течение нескольких столетий оно стоило порой в сорок раз дороже серебра. Но ещё до того, как выплавку можно было увеличить, а хеттам — этим воспользоваться, им пришёл конец. Хеттское царство было разрушено во время беспорядков, последовавших за движением «народов моря», и хеттская монополия на железо была нарушена. Технология выплавки железа быстро распространялась в том числе, конечно, в Ассирию, которая граничила с «железным царством» Урарту. Торговля железом восстановила процветание Ассирии. Открылся путь для новых завоеваний. Вторгшиеся в Грецию дорийские племена обладали железным оружием, именно поэтому они так легко покорили вооруженных бронзой ахейцев. Было железо и у «народов моря», и, когда филистимляне захватывали ханаанское побережье, в сражениях они использовали железное оружие, Но они были не настолько глупы, чтобы раскрывать секрет выплавки железа. Пока им удавалось хранить эту техническую тайну, израильтянам приходилось обороняться более примитивным оружием. Благодаря железу филистимляне не только легко закрепились на побережье, но и обложили данью ближайшие к ним племена. Около двух веков (до прихода к власти Давида в 1013 году до н. э.) им удавалось господствовать над более многочисленными израильскими племенами. | ![]() |
Первым шагом в зарождающейся чёрной металлургии было получение железа путём восстановления его из окиси. Болотная руда перемешивалась с древесным углём и закладывалась в печь. При высокой температуре, создаваемой горением угля, углерод начинал соединяться не только с атмосферным кислородом, но и с тем кислородом, который был связан с атомами железа.
После выгорания угля в печи оставалась так называемая «крица» — комок пористого восстановленного железа с примесью большого количества шлаков. Крицу потом снова разогревали и подвергали обработке ковкой, выколачивая шлак из железа. Полученный брусок железа (в котором всё же оставалось 2—4 % шлака) назывался «кричной болванкой». Долгое время ковка была основным процессом в технологии производства железа, причём, с приданием изделию формы она была связана в последнюю очередь. Ковкой получался сам материал.
Сварное оружие[править | править код]
Сталь производилась уже из готового железа путём насыщения углеродом последнего. При высокой температуре и недостатке кислорода углерод, не успевая окисляться, пропитывал железо. Чем больше было углерода, тем твёрже оказывалась сталь после закалки.
Как можно было заметить, ни один из перечисленных выше сплавов не обладает таким свойством, как упругость. Железный сплав может приобрести это качество, только если в нём возникает чёткая кристаллическая структура, что происходит, например, в процессе застывания из расплава. Проблема же древних металлургов заключалась в том, что расплавить железо они не могли. Для этого требуется разогреть его до 1540 °C, в то время как технологии древности позволяли достичь температур в 1000‑1300 °C. Вплоть до середины XIX века было невозможно расплавить железо и сталь с содержанием углерода менее 0,4 %, так как плавкость железных сплавов снижается по мере уменьшения концентрации углерода.
Таким образом ни железо, ни сталь сами по себе для изготовления оружия не годились. Орудия и инструменты из чистого железа выходили слишком мягкими, а из чистой стали — слишком хрупкими. Потому, чтобы изготовить, например, меч, приходилось делать «бутерброд» из двух пластин железа, между которыми закладывалась стальная пластина. При заточке мягкое железо стачивалось и появлялась стальная режущая кромка.
Такое оружие, сваренное из нескольких слоёв с разными механическими свойствами, называлось сварным. Общими недостатками этой технологии являлись излишняя массивность и недостаточная прочность изделий. Сварной меч не мог пружинить, вследствие чего неизбежно ломался или гнулся при ударе о непреодолимую преграду.
Отсутствием упругости недостатки сварного оружия не исчерпывались. В дополнение к упомянутым недостаткам, его, например, невозможно было «толком» заточить. Железу можно было придать какую угодно остроту (хотя и стачивалось оно быстро), но и тупилась мягкая режущая кромка из железа почти мгновенно. Сталь же точиться не желала — режущая кромка крошилась. Здесь налицо полная аналогия с карандашами — мягкий грифель легко сделать острым, но он сразу затупится, а твёрдый до особой остроты не доведёшь — десять раз сломается. Так что, бритвы приходилось делать из железа и затачивать заново ежедневно.
В целом же сварное оружие не превосходило остротой столовый нож. Уже одно это обстоятельство требовало делать его достаточно массивным для придания удовлетворительных рубящих свойств.
Единственной мерой, позволяющей достичь сочетания остроты и твёрдости в рамках технологии сварки, была закалка изделия уже после его заточки. Применим же этот метод становился в случае, если стальная режущая кромка приваривалась просто к железному обуху, а не заключалась в «бутерброд» из железа. Либо после заточки могли быть закалены клинки, у которых железный сердечник покрывался снаружи сталью. Недостатком такого метода было то, что заточка оказывалась возможна лишь однажды. Когда стальное лезвие повреждалось и тупилось, весь клинок приходилось перековывать.
Тем не менее именно освоение техники сварки — несмотря на все её недостатки — произвело настоящий переворот во всех сферах человеческой деятельности и привело к огромному возрастанию производительных сил. Сварные орудия были вполне функциональны и, при том, общедоступны. Только с их распространением каменные орудия оказались окончательно вытеснены, и наступил век металла.
Железные орудия решительно расширили практические возможности человека. Стало возможным, например, строить рубленные из брёвен дома — ведь железный топор валил дерево уже не в три, как медный, а в 10 раз быстрее, чем каменный. Широкое распространение получило и строительство из тёсаного камня. Он, естественно, употреблялся и в эпоху бронзы, но большой расход сравнительно мягкого и дорогого металла решительно ограничивал такие эксперименты. Значительно расширились также и возможности земледельцев.
Булатная сталь и дамаск[править | править код]
Увидеть железо жидким металлурги смогли только в XIX веке, однако ещё на заре железной металлургии — в начале I тысячелетия до нашей эры — индийские мастера сумели решить проблему получения высокоуглеродистой стали с композитной структурой. Такую сталь называли булатом, но из-за сложности изготовления и отсутствия необходимых материалов в большей части мира эта сталь так и осталась индийским секретом на долгое время.
Более технологичный путь получения упругой стали, при котором не требовались ни особо чистая руда, ни графит, ни специальные печи, был найден в Китае во II веке нашей эры. Сталь перековывали до двенадцати раз, при каждой ковке складывая заготовку вдвое, в результате чего получался отличный оружейный материал, называемый «дамаском», из которого, в частности, делались японские катаны (мечи). Количество слоёв стали рассчитывается по формуле A=2Nx{\displaystyle A=2^{N}x}, где N{\displaystyle N} — количество проковок, а x{\displaystyle x} — изначальное количество видов (слоёв) стали, сковываемой в «бутерброд». При каждой ковке количество слоёв удваивалось, а после 12 проковок количество слоёв достигало 4096, и слои становились неразличимы.
Штукофен[править | править код]
Более высокую, по сравнению с сыродутной печью, ступень в развитии чёрной металлургии представляли собой постоянные высокие печи, называемые в Европе штукофенами. Это действительно была высокая печь — с четырёхметровой трубой для усиления тяги. Мехи штукофена «качались» уже несколькими людьми, а иногда и водяным двигателем. Штукофен имел дверцы, через которые раз в сутки извлекалась крица.
Изобретены штукофены были в Индии в начале первого тысячелетия до новой эры. В начале нашей эры они попали в Китай, а в VII веке вместе с «арабскими» цифрами арабы заимствовали из Индии и эту технологию. В конце XIII века штукофены стали появляться в Германии и Чехии (а ещё до того были на юге Испании) и в течение следующего века распространились по всей Европе.
Производительность штукофена была несравненно выше, чем сыродутной печи — в день он давал до 250 кг железа, а температура в нём оказывалась достаточна для науглероживания части железа до состояния чугуна. Однако штукофенный чугун при остановке печи застывал на её дне, смешиваясь со шлаками, а очищать металл от шлаков умели тогда только ковкой, но как раз ей-то чугун и не поддавался. Его приходилось выбрасывать.
Иногда, впрочем, штукофенному чугуну пытались найти какое-то применение. Например, древние индусы отливали из грязного чугуна гробы, а турки в начале XIX века — пушечные ядра. Трудно судить, сколь хорошими были гробы, но ядра из него получались невысокого качества.
Ядра для пушек из железистых шлаков в Европе отливали ещё в конце XVI века. Из литой брусчатки делались дороги. В Нижнем Тагиле до сих пор сохранились здания с фундаментами из литых шлаковых блоков[7].
Блауофен[править | править код]
Металлурги давно заметили связь между температурой плавления и выходом продукта — чем выше была температура, тем большую часть содержащегося в руде железа удавалось восстановить. Потому рано или поздно им приходила мысль улучшить штукофен — добавить предварительный подогрев воздуха и увеличить высоту трубы. В середине XV века в Европе появились печи нового типа — блауофены, которые сразу преподнесли сталеварам неприятный сюрприз.
Более высокая температура действительно значительно повысила выход железа из руды, но она же повысила и долю железа науглероживающегося до состояния чугуна. Теперь уже не 10 %, как в штукофене, а 30 % выхода составлял чугун — «свиное железо», ни к какому делу не годное. В итоге, выигрыш часто не окупал модернизации.
Блауофенный чугун, как и штукофенный, застывал на дне печи, смешиваясь со шлаками. Он выходил несколько лучшим, так как его самого было больше, следовательно, относительное содержание шлаков выходило меньше, но продолжал оставаться малопригодным для литья. Чугун, получаемый из блауофенов, оказывался уже достаточно прочен, но оставался ещё очень неоднородным. Из него выходили только предметы простые и грубые — кувалды, наковальни, пушечные ядра.
Кроме того, если в сыродутных печах могло быть получено только железо, которое потом науглероживалось, то в штукофенах и блауофенах внешние слои крицы оказывались состоящими из стали. В блауофенных крицах стали было даже больше, чем железа. С одной стороны, это было хорошо, но вот отделить сталь от железа оказалось весьма затруднительно. Содержание углерода становилось трудно контролировать. Только долгой ковкой можно было добиться однородности его распределения.
В своё время, столкнувшись с этими затруднениями, индусы не стали двигаться дальше, а занялись тонким усовершенствованием технологии и пришли к получению булата. Но индусов в ту пору интересовало не количество, а качество продукта. Европейцы, экспериментируя с чугуном, скоро открыли передельный процесс, поднявший металлургию железа на качественно новый уровень.
Доменная печь[править | править код]
Следующим этапом в развитии металлургии стало появление доменных печей. За счёт увеличения размера, предварительного подогрева воздуха и механического дутья, в такой печи всё железо из руды превращалось в чугун, который расплавлялся и периодически выпускался наружу. Производство стало непрерывным — печь работала круглосуточно и не остывала. За день она выдавала до полутора тонн чугуна. Перегнать же чугун в железо в горнах было значительно проще, чем выколачивать его из крицы, хотя ковка все равно требовалась — но теперь уже выколачивали шлаки из железа, а не железо из шлаков.
Хотя найденные в Китае чугунные изделия восходят к V веку до нашей эры[8], самые ранние доменные печи, производящие чугун в «чушках» (слитках), который мог переплавляться в очищенный чугун в вагранках, датируются III—II веками до нашей эры. Подавляющее большинство обнаруженных ранних мест доменного производства относятся к периоду после введения государственной монополии на соль и железорудную промышленность в 117 году до нашей эры (период правления императора У-ди, 141—87 до н. э.) в эпоху династии Хань (202 год до нашей эры — 220 год нашей эры). Большинство железоделательных мест, открытых до 117 года до нашей эры, занимались лишь литьём из заготовок, выплавленных в доменных печах в других районах, отдалённых от населённых пунктов[9][10].
В Европе доменные печи впервые были применены на рубеже XV—XVI веков. На Ближнем Востоке и в Индии эта технология появилась только в XIX веке (в значительной степени, вероятно, потому, что водяной двигатель из-за характерного дефицита воды на Ближнем Востоке не употреблялся). Наличие в Европе доменных печей позволило ей обогнать в XVI веке Турцию если не по качеству металла, то по валу. Это оказало несомненное влияние на исход борьбы, особенно когда оказалось, что из чугуна можно лить пушки.
Георгий Агрикола так описывает средневековую технологию плавки[11]:
![]() | Обычай выдающихся плавильщиков, умеющих управлять четырьмя элементами (имеются в виду земля, воздух, огонь и вода — вне цитаты), таков. Они смешивают в правильных пропорциях руды, содержащие земли, и загружают их в печи. Затем льют нужное количество воды и умело управляют движением воздуха, поступающего из мехов, забрасывая руду туда, где огонь горит с наибольшей силой. Мастер равномерно обрызгивает водой внутреннее пространство печи, слегка увлажняя древесный уголь с тем, чтобы к нему приставали мелкие частицы руды; иначе эти частицы приводятся в движение силой дутья и огня и уносятся вместе с дымом. | ![]() |
Также Агрикола верно объясняет необходимость изменения конструкции печи в зависимости от типа руд[11]:
![]() | Так как природа руд, подлежащих плавке, бывает различной, плавильщикам приходится устраивать горн то выше, то ниже и устанавливать трубу, куда вводятся насадки мехов под меньшим или большим углом для того, чтобы дутье при надобности было более или менее сильным. Если руды нагреваются и плавятся легко, то для работы плавильщиков необходим низкий горн, а труба должна быть установлена под небольшим углом, чтобы дутье было легкое. Наоборот, если руды нагреваются и плавятся медленно, то требуется высокий горн, а труба должна быть установлена с крутым уклоном, чтобы обеспечить сильное дутье. Для руд этого рода нужна весьма горячая печь, в которой сначала расплавляются шлаки, штейны или легкоплавкие камни для того, чтобы руда не могла пригореть к поду горна и закрыть выпускное отверстие. | ![]() |
Передельный процесс[править | править код]
С XVI века в Европе получил распространение так называемый передельный процесс в металлургии — технология, при которой железо ещё при получении за счёт высокой температуры плавления и интенсивного науглероживания перегонялось в чугун, а уже затем, жидкий чугун, освобождаясь от лишнего углерода при отжиге в горнах, превращался в сталь.
Из передельной стали уже можно было изготавливать кривые мечи (например, сабли), чего не позволяла сделать сварная технология.
Применение угля, коксование, пудлингование, горячее дутьё[править | править код]
С начала XVII века европейской кузницей стала Швеция, производившая половину железа в Европе. В середине XVIII века её роль в этом отношении стала стремительно падать в связи с очередным изобретением — применением в металлургии каменного угля.
Прежде всего надо сказать, что до XVIII века включительно каменный уголь в металлургии практически не использовался — из-за высокого содержания вредных для качества продукта примесей, в первую очередь — серы. С XVII века в Англии каменный уголь, правда, начали применять в пудлинговочных печах для отжига чугуна, но это позволяло достичь лишь небольшой экономии древесного угля — большая часть топлива расходовалась на плавку, где исключить контакт угля с рудой было невозможно.
Потребление же топлива в металлургии уже тогда было огромно — домна (доменная печь) пожирала воз угля в час. Древесный уголь превратился в стратегический ресурс. Именно изобилие дерева в самой Швеции и принадлежащей ей Финляндии позволило шведам развернуть производство таких масштабов. Англичане, имевшие меньше лесов (да и те были зарезервированы для нужд флота), вынуждены были покупать железо в Швеции до тех пор, пока не научились использовать каменный уголь. Его ввёл в употребление в XVII веке Клемент Клерк и его мастера кузнечных дел и литья.
С 1709 году в местечке Коулбрукдейл Абрахам Дарби, основатель целой династии металлургов и кузнецов, использовал кокс для получения чугуна из руды в доменной печи. Из него поначалу делали лишь кухонную утварь, которая отличалась от работы конкурентов лишь тем, что её стенки были тоньше, а вес меньше. В 1750-х годах сын Дарби (Абрахам Дарби II) построил ещё несколько домен, и к этому времени его изделия были ещё и дешевле, чем изготовленные на древесном угле. В 1778 году внук Дарби, Абрахам Дарби III, из своего литья построил в Шропшире знаменитый Железный мост, первый мост в Европе, полностью состоящий из металлических конструкций.
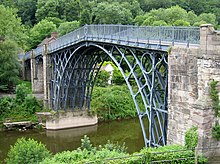
Для дальнейшего улучшения качества чугуна в 1784 году Генри Корт разработал процесс пудлингования. Среди многих металлургических профессий того времени, пожалуй, самой тяжелой была профессия пудлинговщика. Пудлингование было основным способом получения железа почти на протяжении всего XIX века. Это был очень тяжёлый и трудоёмкий процесс. Работа при нём шла так. На подину пламенной печи загружались чушки (слитки) чугуна; чушки расплавляли. По мере выгорания из металла углерода и других примесей температура плавления металла повышалась, и из жидкого расплава начинали «вымораживаться» кристаллы довольно чистого железа. На подине печи собирался комок слипшейся тестообразной массы. Рабочие-пудлинговщики приступали к операции накатывания крицы при помощи железного лома. Перемешивая ломом массу металла, они старались собрать вокруг лома комок, или крицу, железа. Такой комок весил до 50—80 кг и более. Крицу вытаскивали из печи и подавали сразу под молот — для проковки с целью удаления частиц шлака и уплотнения металла[7].
Рост производства и улучшение качества английского металла к концу XVIII века позволило Великобритании полностью отказаться от импорта шведского и российского железа. Развернулось сооружение каналов, позволявших перевозить уголь и металлы.
С 1830 по 1847 год производство металла в Англии возросло более чем в 3 раза. Применение горячего дутья при плавке руды, начавшееся в 1828 году, втрое сократило расход топлива и позволило использовать в производстве низшие сорта каменного угля, С 1826 по 1846 год экспорт железа и чугуна из Великобритании увеличился в 7,5 раза[12].
Конвертерное производство и мартеновские печи[править | править код]
В 1856 году Генри Бессемер получил патент на новую технологию производства стали (бессемеровский процесс). Он изобрёл конвертер — устройство, в котором сквозь жидкий чугун, получаемый в доменных печах, продувался воздух. В конвертере происходит выгорание углерода, растворённого в железе, что позволяет получать сталь в существенно больших количествах, чем это было ранее доступно.
Альтернативой применения конвертера на протяжении XX века являлась мартеновская печь, в которой также происходило дожигание углерода. К концу XX века мартеновские печи стали очевидно устаревшей технологией и были вытеснены кислородно-конвертерным производством стали.
В середине XX века был изобретён турбодетандер, позволяющий снизить затраты на производство кислорода. Кислород стал достаточно дешёвым, чтобы получить массовое применение в сталелитейной промышленности. Продувка расплавленного чугуна кислородом существенно разогревает металл, что упрощает производство (железо не «вымораживается», а остаётся жидким), позволяет также в конвертер сбрасывать металлолом для переплавки, а также в ряде случаев улучшает качество металла за счёт отсутствия растворённого в металле азота.
Электрометаллургия[править | править код]
Способность постоянного электрического тока восстанавливать металлы была обнаружена ещё в самом начале XIX века, однако отсутствие мощных источников электроэнергии ограничивало применение этих процессов лабораторными исследованиями. Появление в начале XX века мощных электростанций позволило создать промышленные технологии электрометаллургии. Изначально такие процессы применялись для производства цветных металлов, но к середине XX века пришли и в чёрную металлургию. Широкое применение нашли процессы электрической рудовосстанавливающей плавки, при которой железная руда, смешенная с незначительным количеством углерода, подвергается воздействию мощной электрической дуги, где происходит электрическое восстановление железа на катоде и выгорание примесей на аноде. Таким способом удаётся получить чугун высокого качества, сократить расход кислорода и снизить уровень выбросов углекислого газа. Передельные электрометаллургические процессы дают возможность плавить чугун в вакууме, в среде защитного газа, в присутствии химически активных легирующих элементов, что позволяет получать легированные стали высокого качества и специальные стали (жаропрочные, радиационно стойкие). Стали, получение которых возможно только электрометаллургическими процессами называют электросталями.
Восстановление водородом[править | править код]
Доменные печи и конвертерное производство является достаточно современным, но весьма грязным для экологии процессом. При том, что большая часть железа получается в кислородно-конвертерном производстве, велики и выбросы углекислого и угарного газов в атмосферу. Модной альтернативой становится прямое восстановление железа из руды водородом. При этом образующиеся частички железа расплавляются в электрических печах, после чего добавляется углерод и получается сталь.
Кузнецы-любители[править | править код]
Первыми производство железных изделий организовали кузнецы-любители — обычные крестьяне, промышлявшие таким ремеслом в свободное от обработки земли время. Кузнец сам находил «руду» (болотная руда вблизи ржавого болота или красный песок), сам выжигал уголь, сам строил сыродутную печь и выплавлял железо, сам ковал, сам обрабатывал.
Умение мастера на данном этапе закономерно было ограничено выковыванием изделий самой простой формы. Инструментарий же его состоял из мехов, каменных молота и наковальни и точильного камня. Железные орудия производились с помощью каменных инструментов.
Если удобные для разработки залежи руды имелись поблизости, то и целая деревня могла заниматься производством железа, но такое было возможным только при наличии устойчивой возможности выгодного сбыта продукции, чего практически не могло быть в условиях натурального хозяйства.
При такой организации производства железа, никогда не удавалось за его счёт полностью покрыть все потребности в самом простом оружии и самых необходимых орудиях труда. Из камня продолжали изготавливаться топоры, из дерева — гвозди и плуги. Металлические доспехи оставались недоступными даже для вождей. Концентрация железных изделий составляла всего порядка 200 граммов на душу населения[источник не указан 1118 дней].
На таком уровне доступности железа находились в начале нашей эры наиболее отсталые племена среди бриттов, германцев и славян. В XII‑XIII веке прибалты и финны сражаясь с крестоносцами пользовались ещё каменным и костяным оружием. Все эти народы умели уже делать железо, но ещё не могли получить его в необходимом количестве.[источник не указан 1118 дней]
Профессиональные кузнецы[править | править код]
Следующим этапом развития чёрной металлургии были профессиональные кузнецы, которые всё ещё сами выплавляли металл, но на добычу железоносного песка и выжигания угля чаще уже отправляли других мужиков — в порядке натурального обмена. На этом этапе кузнец, обычно, уже имел помощника-молотобойца и как-то оборудованную кузницу.
С появлением кузнецов концентрация железных изделий возрастала в 4‑5 раз. Теперь уже каждый крестьянский двор мог быть обеспечен персональным ножом и топором. Возрастало и качество изделий. Кузнецы профессионалы, как правило, владели техникой сварки и могли вытягивать проволоку. В принципе, такой умелец мог получить и дамаск, если знал как, но производство дамаскового оружия требовало такого количества железа, что не могло ещё быть сколько-то массовым.
В XVIII-XIX веках деревенские кузнецы умудрялись даже изготовлять стволы к нарезному оружию, но в этот период они уже пользовались оборудованием, которое сделали не сами. Некоторого масштаба перенос ремесленного производства из города в деревню становился возможным на таком этапе развития города, когда стоимость даже довольно сложного оборудования оказывалась незначительной.
Средневековые же деревенские кузнецы сами делали свои орудия труда. Как умели. Поэтому рядовой мастер обычно преуспевал в изготовлении предметов простой плоской формы, но положительно затруднялся, когда требовалось изготовить трёхмерное изделие, или состыковать несколько изделий между собой — что, например, требовалось для создания надёжного шлема. Изготовить же такое сложное изделие, как спусковой механизм для арбалета, деревенскому кузнецу было непосильно — для этого ведь потребовались бы даже измерительные устройства.
Не было у кустарных кузнецов и специализации — и мечи, и иголки, и подковы делал один и тот же мастер. Более того, во все времена сельские кузнецы были заняты в первую очередь именно изготовлением наиболее необходимых односельчанам простейших производственных и бытовых орудий, но не оружия.
Впрочем, последнее отнюдь не отменяет того обстоятельства, что в примитивных культурах даже самый заурядный кузнец считался несколько сродни колдуну, хотя, более адекватно его можно уподобить художнику. Выковывание даже обычного меча было настоящим искусством.
Теоретически всё выглядело просто: надо только наложить одна на другую три полоски металла, проковать их, и клинок готов. На практике, однако, возникали проблемы — с одной стороны надо было добиться прочной сварки и даже взаимопроникновения слоев, а с другой, нельзя было нарушать равномерность толщины слоя (а она-то и была — с лист бумаги) и, тем более, допустить, чтобы слой разорвался. А, ведь, обработка производилась тяжёлым молотом.
До разделения труда между городом и деревней годовое производство железа не превышало 100 граммов в год на человека, форма изделий была очень простой, а качество — низким, и, когда описывается вооружение какого-нибудь варяга, систематически упускается из вида, что речь идёт об оружии вождя, откопанном в его кургане. Варвары, которым курганы не полагались, вооружались существенно проще. На данном уровне развития производительных сил (характерном, например, для галлов, франков, норманнов, Руси X века) тяжёлое вооружение могло иметься только у аристократии — не более одного воина в броне на 1000 человек населения.
На новый уровень металлообрабатывающая промышленность вступила только тогда, когда стало возможным разделение труда и возникновение специальностей. Мастер железо покупал, причём уже нужного качества, покупал инструменты, необходимые по его профилю, и нанимал подмастерьев. Если уж он и делал ножи, то сдавал их на реализацию ящиками. Если делал мечи, то не по два в год, а по четыре в неделю. И, естественно, обладал большим опытом в их изготовлении.
Но для возникновения специализации непременно требовался город — хоть на несколько тысяч жителей — чтобы мастер мог всё купить и продать. Даже очень крупные призамковые посёлки (а их население тоже иногда достигало нескольких тысяч человек) не давали такой возможности — ведь в них не только ничего не производилось на продажу в другие поселения, но и отсутствовал даже внутренний товарообмен.
Чем более был развит обмен, тем больше могло быть мастеров и их специализаций, сформироваться разделение труда. Но для значительного развития обмена требовались деньги и сравнительная стабильность.
Ещё больший прогресс мог быть достигнут организацией мануфактуры, но вокруг неё требовалось выстроить уже 50-тысячный город, и наличие ещё нескольких таких же поблизости.
Тем не менее, даже после сосредоточения ремесленного производства в городах, колоритная фигура кузнеца оставалась непременным элементом пасторального ландшафта вплоть до начала, а кое-где и до середины XX века. Долгое время крестьяне просто не имели возможности покупать городские изделия. На ранних этапах развития обмена квалифицированные ремесленники обслуживали только господствующие классы — в первую очередь военные сословия.
После распространения штукофенов[править | править код]
Кустарное производство железа, однако, перестало практиковаться сразу после распространения штукофенов. Кузнецы начали покупать железо в слитках, а ещё чаще — железный лом, на предмет перековки мечей на орала.
Когда же развитие товарности хозяйства сделало ремесленные изделия доступными широким массам, кузнецы ещё долго занимались починкой сделанных в городах орудий.
Параллельно с решением организационных моментов улучшение методов обработки металлов требовало и совершенствования техники. Поскольку же основным методом была ковка, то усовершенствованию подлежали в первую очередь молоты.
Дело было в том, что, если ковка осуществлялась ручным молотом, то и размер изделия оказывался ограничен физическими возможностями кузнеца. Человек был способен отковать деталь весом не более нескольких килограммов. В большинстве случаев этого оказывалось достаточно, но при изготовлении, скажем, деталей осадных машин без механического молота, приводимого в движение водяным колесом, мулами или рабочими, было уже не обойтись.
Проблема выковывания массивных (до нескольких центнеров) деталей была решена ещё в античности, но в период средних веков она обрела новую остроту, так как крицы, получаемые из штукофенов, тоже нельзя было отковать кувалдой.
Конечно, можно было делить их на небольшие части, но, при этом, в каждой оказалось бы своё, причём неизвестное, содержание углерода, а потом, для изготовления мало-мальски крупного изделия полученные куски пришлось бы сковывать обратно.
Всё это было крайне невыгодно. Ковать крицу надо было целиком. Потому, штукофен по-хорошему требовалось комплектовать даже не одной, а тремя водяными машинами — одна качала мехи, другая — орудовала молотом, третья — откачивала воду из шахты. Без третьей тоже было никак — кустарными заготовками штукофен рудой было не обеспечить.
Впрочем, объёмы производства зависели не столько от технологий, сколько от организации труда. Если металлург не отвлекался на другие задачи, то и сыродутных печей он мог наделать куда больше. Так, в Риме производство достигло 1.5 килограмма на человека в год, и этого не хватало — железо в Рим возили даже из Китая. В Европе же и Азии даже с использованием штукофенов производство редко достигало килограмма. Но с появлением доменных печей в Европе этот показатель разом утроился, а в Шв
Как из железной окалины получить железо
Смесь оксидов железа, образовывающаяся при взаимодействии кислорода с раскалённым металлом, имеет обобщённое название — железная окалина. Она состоит из Fe3O4, FeO и Fe2O3 (магнетита, вьюстита и гематита соответственно) и представлена двумя легкоотделяемыми друг от друга слоями. При их суммарной толщине до 40 нм окалина невидима невооружённому взгляду, свыше 40 и до 500 нм — выдаёт себя цветами побежалости (радужным отливом). Постоянный же окрас появляется, если слой железной окалины на металле превышает 500 нм.
Состав
Наружный слой оксида железа — гематит. Он обладает большой твёрдостью (1030 ед. по шкале Виккерса), абразивностью и очень плохо растворяется в кислотах. Под ним в условиях частичной нехватки кислорода формируется более мягкий и почти нерастворимый в кислотах магнетит. Ближе всего к металлу находится рыхлый и мягкий вьюстит, который легко поддается устранению механическим путём или кислотным травлением.
Толщина каждого из трёх слоёв зависит от температуры обработки стали. Так, при превышении порога в 570 °C образуется чётко выраженная трёхслойная структура окалины. Дальнейшее повышение температуры ведёт к увеличению толщины вьюстита. Если же сталь обрабатывается при температурах ниже 570 °C, то в составе окалины преобладают магнетит и гематит.
По цвету железной окалины можно определить температуру обработки стали. Так, при температуре в 700–750 °C в составе окалины больше гематита, из-за чего она приобретает рыжевато-красный оттенок. Образовавшийся при высокотемпературном (900–1000 °C) прокате слой оксидов из-за более высокого процента вьюстита становится чёрным.
Особенности
Твёрдость окалины сочетается с её хрупкостью, из-за чего вкрапления оксида внутри структуры металла резко понижают его эксплуатационные характеристики. По этой же причине железная окалина не может быть использована в качестве защитного покрытия, хоть она и не взаимодействует с кислородом. Более того, в месте скола оксидов наблюдается усиленное окисление стали, что происходит из-за разности потенциалов окалины и стали. По этой причине её удаляют с готового проката.
Удаление окалины
Слой оксидов железа с прокатной стали удаляют со стальной заготовки несколькими способами.
- механическая;
- химическая;
- электрохимическая.
Возможно также сочетание вариантов.
Механическое воздействие на прокат сводится к пропуску проволоки или листа с окалиной через ряд роликов. При этом достигается частое изгибание заготовки, под воздействием которого железная окалина рассыпается на отдельные чешуйки и осыпается с металла. Для финишной очистки могут быть использованы абразивы, наждачные ленты, щётки из проволоки.
Достоинством этой технологии является сравнительная дешевизна и экологичность. Но поскольку отказ от смазки при такой обработке нецелесообразен, это приводит к замасливанию железной окалины, что затрудняет дальнейшую её переработку.
Химический и электрохимический способы очистки стали называют травлением. Для этих целей используются серная и соляная кислоты, реже — фосфорная, азотная, плавиковая или их смесь. Главными недостатками такого способа является одноразовое использование травильных растворов (не восстанавливаются) и низкий спрос на побочный продукт преобразования окалины — железный купорос. По этой причине травление применяется довольно редко, и ему обычно предшествует механическая очистка проката от окалины.
Применение окалины
Опытными кузнецами давно было примечено повышение сопротивляемости металла коррозии при формировании на нём тонкого слоя окалины. Сейчас же воронение оружейной стали используется лишь в качестве декоративной отделки. Её цвет зависит от способа обработки (кислота, щёлочь, температура) и толщины оксидной плёнки, составляющей от 1 до 10 мкм.
Прокатная окалина, удельный вес которой достигает 3% от общего веса готовых изделий, является ценным сырьём для металлургического производства за счёт высокого содержания (до 75%) в ней железа. Основное направление её переработки — очистка от примесей и восстановление, после которого она превращается в низкоуглеродистую сталь.
Некоторые составы окалины успешно применяются в качестве красящих пигментов и активно используются в строительстве. Также из окалины производится железный порошок, применяемый в металлургии, при изготовлении самонагревающихся смесей и даже в пищевой промышленности.
Химический состав этого отхода металлургической промышленности стандартизирован. Её стоимость может колебаться в зависимости от преобладания определённых видов окислов и количества примесей. Усреднённая цена на начало 2019 года составляла 50 американских долларов за тонну железной окалины.
В свободном состоянии железо — серебристо-белый металл с сероватым оттенком. Чистое железо пластично, обладает ферромагнитными свойствами. На практике обычно используются сплавы железа — чугуны и стали.
Fe — самый главный и самый распространенный элемент из девяти d-металлов побочной подгруппы VIII группы. Вместе с кобальтом и никелем образует «семейство железа».
При образовании соединений с другими элементами чаще использует 2 или 3 электрона (В = II, III ).
Железо, как и почти все d-элементы VIII группы, не проявляет высшую валентность, равную номеру группы. Его максимальная валентность достигает VI и проявляется крайне редко.
Наиболее характерны соединения, в которых атомы Fe находятся в степенях окисления +2 и +3.
Железо – химический элемент
1. Положение железа в периодической таблице химических элементов и строение его атома
Железо — это d- элемент VIII группы; порядковый номер – 26; атомная масса Ar ( Fe ) = 56; состав атома: 26-протонов; 30 – нейтронов; 26 – электронов.
Схема строения атома:
Электронная формула: 1s 2 2s 2 2p 6 3s 2 3p 6 3d 6 4s 2
Металл средней активности, восстановитель:
Fe 0 -2 e — → Fe +2 , окисляется восстановитель
Fe 0 -3 e — → Fe +3 , окисляется восстановитель
Основные степени окисления: +2, +3
2. Распространённость железа
Железо – один из самых распространенных элементов в природе . В земной коре его массовая доля составляет 5,1%, по этому показателю оно уступает только кислороду, кремнию и алюминию. Много железа находится и в небесных телах, что установлено по данным спектрального анализа. В образцах лунного грунта, которые доставила автоматическая станция “Луна”, обнаружено железо в неокисленном состоянии.
Железные руды довольно широко распространены на Земле. Названия гор на Урале говорят сами за себя: Высокая, Магнитная, Железная. Агрохимики в почвах находят соединения железа.
Железо входит в состав большинства горных пород. Для получения железа используют железные руды с содержанием железа 30-70% и более.
Основными железными рудами являются :
магнетит (магнитный железняк) – Fe3O4 содержит 72% железа, месторождения встречаются на Южном Урале, Курской магнитной аномалии:
гематит (железный блеск, кровавик)– Fe2O3содержит до 65% железа, такие месторождения встречаются в Криворожском районе:
лимонит (бурый железняк) – Fe2O3*nH2O содержит до 60% железа, месторождения встречаются в Крыму:
пирит (серный колчедан, железный колчедан, кошачье золото) – FeS2 содержит примерно 47% железа, месторождения встречаются на Урале.
3. Роль железа в жизни человека и растений
Биохимики открыли важную роль железа в жизни растений, животных и человека. Входя в состав чрезвычайно сложно построенного органического соединения, называемого гемоглобином, железо обусловливает красную окраску этого вещества, от которого в свою очередь, зависит цвет крови человека и животных. В организме взрослого человека содержится 3 г чистого железа, 75% которого входит в состав гемоглобина. Основная роль гемоглобина – перенос кислорода из легких к тканям, а в обратном направлении – CO2.
Железо необходимо и растениям. Оно входит в состав цитоплазмы, участвует в процессе фотосинтеза. Растения, выращенные на субстрате, не содержащем железа, имеют белые листья. Маленькая добавка железа к субстрату – и они приобретают зеленый цвет. Больше того, стоит белый лист смазать раствором соли, содержащей железо, и вскоре смазанное место зеленеет.
Так от одной и той же причины – наличия железа в соках и тканях – весело зеленеют листья растений и ярко румянятся щеки человека.
4. Физические свойства железа.
Железо – это серебристо-белый металл с температурой плавления 1539 о С. Очень пластичный, поэтому легко обрабатывается, куется, прокатывается, штампуется. Железо обладает способностью намагничиваться и размагничиваться, поэтому применяется в качестве сердечников электромагнитов в различных электрических машинах и аппаратах. Ему можно придать большую прочность и твердость методами термического и механического воздействия, например, с помощью закалки и прокатки.
Различают химически чистое и технически чистое железо. Технически чистое железо, по сути, представляет собой низкоуглеродистую сталь, оно содержит 0,02 -0,04% углерода, а кислорода, серы, азота и фосфора – еще меньше. Химически чистое железо содержит менее 0,01% примесей. Химически чистое железо – серебристо-серый, блестящий, по внешнему виду очень похожий на платину металл. Химически чистое железо устойчиво к коррозии и хорошо сопротивляется действию кислот. Однако ничтожные доли примесей лишают его этих драгоценный свойств.
Восстановлением из оксидов углём или оксидом углерода (II), а также водородом:
6. Химические свойства железа
Как элемент побочной подгруппы железо может проявлять несколько степеней окисления. Мы рассмотрим только соединения, в которых железо проявляет степени окисления +2 и +3. Таким образом, можно говорить, что у железа имеется два ряда соединений, в которых оно двух- и трехвалентно.
1) На воздухе железо легко окисляется в присутствии влаги (ржавление):
2) Накалённая железная проволока горит в кислороде, образуя окалину — оксид железа (II,III) — вещество чёрного цвета:
3) При высокой температуре (700–900°C) железо реагирует с парами воды:
4) Железо реагирует с неметаллами при нагревании:
5) Железо легко растворяется в соляной и разбавленной серной кислотах при обычных условиях:
6) В концентрированных кислотах – окислителях железо растворяется только при нагревании
На холоде концентрированные азотная и серная кислоты пассивируют железо!
7) Железо вытесняет металлы, стоящие правее его в ряду напряжений из растворов их солей.
8) Качественные реакции на
Основная часть получаемого в мире железа используется для получения чугуна и стали — сплавов железа с углеродом и другими металлами. Чугуны содержат около 4% углерода. Стали содержат углерода менее 1,4%.
Чугуны необходимы для производства различных отливок — станин тяжелых машин и т.п.
Стали используются для изготовления машин, различных строительных материалов, балок, листов, проката, рельсов, инструмента и множества других изделий. Для производства различных сортов сталей применяют так называемые легирующие добавки, которыми служат различные металлы: М n , С r , Мо и другие, улучшающие качество стали.
Задания для закрепления
№1. Составьте уравнения реакций получения железа из его оксидов Fe2O3 и Fe3O4 , используя в качестве восстановителя:
а) водород;
б) алюминий;
в) оксид углерода (II).
Для каждой реакции составьте электронный баланс.
№2. Осуществите превращения по схеме:
Fe2O3 -> Fe — +h3O, t -> X — +CO, t -> Y — +HCl -> Z
Назовите продукты X, Y, Z?
Железо. Описание, свойства, происхождение и применение металла
Чистое железо (99,97%), очищенное методом электролиза
Железо — ковкий металл серебристо-белого цвета с высокой химической реакционной способностью: железо быстро корродирует при высоких температурах или при высокой влажности на воздухе. В чистом кислороде железо горит, а в мелкодисперсном состоянии самовозгорается и на воздухе. Обозначается символом Fe (лат. Ferrum). Один из самых распространённых в земной коре металлов (второе место после алюминия).
СТРУКТУРА
Две модификации кристаллической решетки железа
Для железа установлено несколько полиморфных модификаций, из которых высокотемпературная модификация — γ-Fe(выше 906°) образует решетку гранецентрированного куба типа Сu (а0 = 3,63), а низкотемпературная — α-Fe-решетку центрированного куба типа α-Fe (a0 = 2,86).
В зависимости от температуры нагрева железо может находиться в трех модификациях, характеризующихся различным строением кристаллической решетки:
- В интервале температур от самых низких до 910°С —а-феррит (альфа-феррит), имеющий строение кристаллической решетки в виде центрированного куба;
- В интервале температур от 910 до 1390°С — аустенит, кристаллическая решетка которого имеет строение гранецентрированного куба;
- В интервале температур от 1390 до 1535°С (температура плавления) — д-феррит (дельта-феррит). Кристаллическая решетка д-феррита такая же, как и а-феррита. Различие между ними только в иных (для д-феррита больших) расстояниях между атомами.
При охлаждении жидкого железа первичные кристаллы (центры кристаллизации) возникают одновременно во многих точках охлаждаемого объема. При последующем охлаждении вокруг каждого центра надстраиваются новые кристаллические ячейки, пока не будет исчерпан весь запас жидкого металла.
В результате получается зернистое строение металла. Каждое зерно имеет кристаллическую решетку с определенным направлением его осей.
При последующем охлаждении твердого железа при переходах д-феррита в аустенит и аустенита в а-феррит могут возникать новые центры кристаллизации с соответствующим изменением величины зерна
СВОЙСТВА
Железная руда
В чистом виде при нормальных условиях это твердое вещество. Оно обладает серебристо-серым цветом и ярко выраженным металлическим блеском. Механические свойства железа включают в себя уровень твердости по шкале Мооса. Она равна четырем (средняя). Железо обладает хорошей электропроводностью и теплопроводностью. Последнюю особенность можно ощутить, дотронувшись до железного предмета в холодном помещении. Так как этот материал быстро проводит тепло, он за короткий промежуток времени забирает большую его часть из вашей кожи, и поэтому вы ощущаете холод.
Дотронувшись, к примеру, до дерева, можно отметить, что его теплопроводность намного ниже. Физические свойства железа — это и его температуры плавления и кипения. Первая составляет 1539 градусов по шкале Цельсия, вторая — 2860 градусов по Цельсию. Можно сделать вывод, что характерные свойства железа — хорошая пластичность и легкоплавкость. Но и это еще далеко не все. Также в физические свойства железа входит и его ферромагнитность. Что это такое? Железо, магнитные свойства которого мы можем наблюдать на практических примерах каждый день, — единственный металл, обладающий такой уникальной отличительной чертой. Это объясняется тем, что данный материал способен намагничиваться под действием магнитного поля. А по прекращении действия последнего железо, магнитные свойства которого только что сформировались, еще надолго само остается магнитом. Такой феномен можно объяснить тем, что в структуре данного металла присутствует множество свободных электронов, которые способны передвигаться.
ЗАПАСЫ И ДОБЫЧА
Железо — один из самых распространённых элементов в Солнечной системе, особенно на планетах земной группы, в частности, на Земле. Значительная часть железа планет земной группы находится в ядрах планет, где его содержание, по оценкам, около 90 %. Содержание железа в земной коре составляет 5 %, а в мантии около 12 %.
Железо
В земной коре железо распространено достаточно широко — на его долю приходится около 4,1 % массы земной коры (4-е место среди всех элементов, 2-е среди металлов). В мантии и земной коре железо сосредоточено главным образом в силикатах, при этом его содержание значительно в основных и ультраосновных породах, и мало — в кислых и средних породах.
Известно большое число руд и минералов, содержащих железо. Наибольшее практическое значение имеют красный железняк (гематит, Fe2O3; содержит до 70 % Fe), магнитный железняк (магнетит, FeFe2O4, Fe3O4; содержит 72,4 % Fe), бурый железняк или лимонит (гётит и гидрогётит, соответственно FeOOH и FeOOH·nH2O). Гётит и гидрогётит чаще всего встречаются в корах выветривания, образуя так называемые «железные шляпы», мощность которых достигает несколько сотен метров. Также они могут иметь осадочное происхождение, выпадая из коллоидных растворов в озёрах или прибрежных зонах морей. При этом образуются оолитовые, или бобовые, железные руды. В них часто встречается вивианит Fe3(PO4)2·8H2O, образующий чёрные удлинённые кристаллы и радиально-лучистые агрегаты.
Содержание железа в морской воде — 1·10−5-1·10−8 %
В промышленности железо получают из железной руды, в основном из гематита (Fe2O3) и магнетита (FeO·Fe2O3).
Существуют различные способы извлечения железа из руд. Наиболее распространённым является доменный процесс.
Первый этап производства — восстановление железа углеродом в доменной печи при температуре 2000 °C. В доменной печи углерод в виде кокса, железная руда в виде агломерата или окатышей и флюс (например, известняк) подаются сверху, а снизу их встречает поток нагнетаемого горячего воздуха.
Кроме доменного процесса, распространён процесс прямого получения железа. В этом случае предварительно измельчённую руду смешивают с особой глиной, формируя окатыши. Окатыши обжигают, и обрабатывают в шахтной печи горячими продуктами конверсии метана, которые содержат водород. Водород легко восстанавливает железо, при этом не происходит загрязнения железа такими примесями, как сера и фосфор, которые являются обычными примесями в каменном угле. Железо получается в твёрдом виде, и в дальнейшем переплавляется в электрических печах. Химически чистое железо получается электролизом растворов его солей.
ПРОИСХОЖДЕНИЕ
Самородное железо
Происхождение теллурическое (земное) железо редко встречается в базальтовыхлавах (Уифак, о. Диско, у западного берега Гренландии, вблизи г. Касселя Германия). В обоих пунктах с ним ассоциируют пирротин (Fe1-xS) и когенит (Fe3C), что объясняют как восстановление углеродом (в том числе и из вмещающих пород), так и распадом карбонильных комплексов типа Fe(CO)n. В микроскопических зернах оно не раз устанавливалось в измененных (серпентинизированных) ультраосновных породах также в парагенезисе с пирротином, иногда с магнетитом, за счет которых оно и возникает при восстановительных реакциях. Очень редко встречается в зоне окисления рудных месторождений, при образовании болотных руд. Зарегистрированы находки в осадочных породах, связываемые с восстановлением соединений железа водородом и углеводородами.
Почти чистое железо найдено в лунном грунте, что связывают как с падениями метеоритов, так и с магматическими процессами. Наконец, два класса метеоритов — железокаменные и железные содержат природные сплавы железа в качестве породообразующего компонента.
ПРИМЕНЕНИЕ
Кольцо из железа
Железо — один из самых используемых металлов, на него приходится до 95 % мирового металлургического производства.
Железо является основным компонентом сталей и чугунов — важнейших конструкционных материалов.
Железо может входить в состав сплавов на основе других металлов — например, никелевых.
Магнитная окись железа (магнетит) — важный материал в производстве устройств долговременной компьютерной памяти: жёстких дисков, дискет и т. п.
Ультрадисперсный порошок магнетита используется во многих чёрно-белых лазерных принтерах в смеси с полимерными гранулами в качестве тонера. Здесь одновременно используется чёрный цвет магнетита и его способность прилипать к намагниченному валику переноса.
Уникальные ферромагнитные свойства ряда сплавов на основе железа способствуют их широкому применению в электротехнике для магнитопроводов трансформаторов и электродвигателей.
Хлорид железа(III) (хлорное железо) используется в радиолюбительской практике для травления печатных плат.
Семиводный сульфат железа (железный купорос) в смеси с медным купоросом используется для борьбы с вредными грибками в садоводстве и строительстве.
Железо применяется в качестве анода в железо-никелевых аккумуляторах, железо-воздушных аккумуляторах.
Водные растворы хлоридов двухвалентного и трёхвалентного железа, а также его сульфатов используются в качестве коагулянтов в процессах очистки природных и сточных вод на водоподготовке промышленных предприятий.
Железо (англ. Iron) — Fe
Молекулярный вес | 55.85 г/моль |
Происхождение названия | возможно англо-саксонского происхождения |
IMA статус | действителен, описан впервые до 1959 (до IMA) |
КЛАССИФИКАЦИЯ
Hey’s CIM Ref1.57
Strunz (8-ое издание) | 1/A.07-10 |
Nickel-Strunz (10-ое издание) | 1.AE.05 |
Dana (7-ое издание) | 1.1.17.1 |
ФИЗИЧЕСКИЕ СВОЙСТВА
Цвет минерала | железно-черный |
Цвет черты | серый |
Прозрачность | непрозрачный |
Блеск | металлический |
Спайность | несовершенная по {001} |
Твердость (шкала Мооса) | 4,5 |
Излом | в зазубринах |
Прочность | ковкий |
Плотность (измеренная) | 7.3 — 7.87 г/см3 |
Радиоактивность (GRapi) | 0 |
Магнетизм | ферромагнетик |
ОПТИЧЕСКИЕ СВОЙСТВА
Тип | изотропный |
Цвет в отраженном свете | белый |
Люминесценция в ультрафиолетовом излучении | не флюоресцентный |
КРИСТАЛЛОГРАФИЧЕСКИЕ СВОЙСТВА
Точечная группа | m3m (4/m 3 2/m) — изометрический — гексаоктаэдральный |
Пространственная группа | Im3m (I4/m 3 2/m) |
Сингония | кубическая |
Параметры ячейки | a = 2.8664Å |
Двойникование | (111) также в пластинчатых массах {112} |
Морфология | в маленьких пузырьках |
Интересные статьи:
mineralpro.ru 13.07.2016Железо — Знаешь как
Изготовление изделий из железа (гл. обр. украшений) началось в первой половине 3-го тысячелетия до н. э. Во 2-м тысячелетии до н. э. был создан способ произ-ва достаточно твердого металла. В Европе и в Древней Руси до середины 14 в. Ж. получали в сыродутных горнах прямым восстановлением руды древесным углем (сыродутный процесс), получая губку (крицу), из к-рой затем выковывали различные изделия. В дальнейшем, по мере усовершенствования способов дутья и увеличения высоты плавильных печей, Ж. науглероживалось , превращаясь в чугун, к-рый вначале считали отходом произ-ва.
Постепенно чугун научились переделывать в сталь. Такой двухступенчатый передел оказался более экономичным и производительным и с 15—16 вв. почти полностью заменил одноступенчатую схему произ-ва Ж. и стали. В середине 19 в. были разработаны бессемеровский, томасов-ский и мартеновский способы передела чугуна в сталь, пополнившиеся впоследствии электросталеплавильным, кислородно-конверторным и др. способами. По содержанию в земной коре (4,65%) Ж. занимает четвертое место после кислорода, кремния и алюминия. В земных глубинах содержание его возрастает. В земной коре Ж. сформировалось в различные минералы, к-рых насчитывается около 300: окислы, сульфиды, силикаты, карбонаты, фосфаты и т. д. Важнейшие рудные минералы: магнетит Fe304, гематит Fe203, лимонит Fe20 • Н20, сидерит FeC03, а также соединения с серой и мышьяком. В виде гидроокисей Ж. накапливается во мн. морских и континентальных осадках, образуя осадочные руды.
Железо это
Железо — в виде теллурического земного или метеоритного — встречается в природе редко. Ж.— пластичный металл, легко поддается ковке, прокатке, штампованию и волочению. Его кристаллические модификации: альфа-, гамма- и дельта-железо. До т-ры 769° С стойко альфа-железо, выше т-ры 769° С (Кюри точка) оно сохраняет кристаллическую структуру, однако теряет ферромагнетизм, переходя в дельта-железо; при т-ре 911° С переходит в гамма-железо, а при т-ре 1400° С гамма-железо превращается в дельта-железо. Немагнитную модификацию железа, стойкую в интервале т-р 769—911° С, нередко наз. бета-железом. Однако его структура тождественна высокотемпературной модификации дельта-железа и не может рассматриваться как самостоятельная. Внешняя электронная оболочка атома Ж. имеет 3d⁶4s² электронов. Наличие незаполненного 3d слоя и его относительные размеры определяют многие физ. и хим. св-ва элемента.Так, взаимодействие нескомпенсированных спинов четырех из шести электронов соседних атомов на небольших расстояниях, свойственных альфа-железу, создает области спонтанной намагниченности (домены), определяющие ферромагнетизм. С увеличением межатомных расстояний обменное взаимодействие ослабляется, что приводит к раз упорядочению областей и исчезновению ферромагнетизма при т-ре 769° С. Сосредоточение четырех электронов в металле и их взаимодействие с катионами приводят к перекрытию d6 орбиталей и появлению направленных связей, свойственных объемноцентрированной кубической структуре альфа- в дельта-железа. Если перекрытия в гамма-железе нет, координационное число увеличивается до 12. Физ. св-ва чистого Ж.: tпл 1536° С; tкип 2880° С; коэфф. теплопровод кости (т-ра 25° С) 0,177 кал/см •сек • град-1, ср. удельная теплоемкость (т-ра 0—1000° С) 0,153 кал/г • град; температурный коэфф. линейного расширения (т-ра 20° С)
11,7 • 10-6 град-1 удельное электрическое сопротивление (т-ра 20° С) 9.7 • 10 ом • см; температ. коэфф. электр. сопротивления (0—100° С) 6,51 • 10-3 град-1 . Многие св-ва зависят от чистоты металла.
В хим. отношении железо— металл средней активности: если нет влаги, его компактные образцы не реагируют заметно даже с такими окислителями, как кислород, сера, хлор и бром. Только высокодисперсное (пирофорное) Ж. может самовоспламеняться. При нагревании интенсивность взаимодействия быстро возрастает. Из кислородных соединений известны: FeO (точнее вюстит FexO — нестехиометрическое соединение нерем. состава, стойкое выше т-ры 572° С), Fe304 и Fe203. При т-ре 200—300° С на воздухе Ж. покрывается плотной окисной пленкой, защищающей его от коррозии (см. Коррозия металлов). Чистое Ж. при обычных т-рах стойко на воздухе и в воде. Техническое Ж. и железа сплавы под воздействием паров воды, углекислого газа и кислорода корродируют, покрываясь хрупким пористым слоем гидроокиси FeO x x nН20 — ржавчиной, не защищающей металл от коррозии. От нее ежегодно теряется около 30% добываемого Ж. и стали, из к-рых в виде металлолома идут в переплав, а теряется безвозвратно. Растворимость углерода в альфа-железе при комнатной т-ре — около 2 • 10-5 %, а при т-ре 738° С составляет 0,02%. В гамма-железе при т-ре 1153° С растворяется до 2,11% С.
Твердый раствор углерода в альфа-железе (феррит) и в гамма-железе (аустенит) являются растворами внедрения. В зависимости от содержания углерода сплавы Ж. подразделяют на стали и чугуны. При быстром охлаждении аустенита образуется пересыщенный твердый раствор углерода в альфа-железе (мартенсит) , обладающий высокой твердостью и хрупкостью. Последующий отпуск (нагрев до т-ры 500—550° С и выдержка) позволяет получить регулируемое сочетание мех. прочности и пластичности. При сравнительно быстром охлаждении из железоуглеродистых расплавов выделяются карбиды: Fe3С (цементит), реже Fe2C (эпсилон-карбид), а при медленном — графит. Наиболее стойки нитриды Fe4N и Fe2N. Соединения Ж. с водородом (гидриды) малостойки. Соединения с серой имеют перем. состав: в FexS содержится от 50 до 53,3 ат.% S.
При нагревании с кремнием, фосфором, алюминием и титаном Ж. образует соответственно силициды, фосфиды, алюминиды и титаниды. Ж. хорошо растворяется в разбавленных к-тах и практически не растворяется в щелочах. Водные растворы его солей имеют кислую реакцию. Ж. склонно к образованию комплексных соединений. Чистое Ж. получают восстановлением из окислов (железо пирофорное), электролизом водных растворов его солей (железо электролитическое) , разложением пента кар бонила Fe (СО)5 при нагревании до т-ры 250° С (см. Железо карбонильное) . Для произ-ва особо чистого железа (99,99% Fe) прибегают к зонной плавке и др. спец. способам. Технически чистое Ж. (армко-железо), содержащее около 0,16% примесей (углерода, кремния, марганца, фосфора, серы и др.), выплаваяют, окисляя компоненты чугуна, в мартеновских, двухванных сталеплавильных печах и в кислородных конверторах.
Сварочное, или кричное, Железо получают, окисляя примеси малоуглеродистой стали железистым шлаком при т-ре 1350° С или восстановлением из руд твердым углеродом. Восстановлением при т-ре до 1200 ° С получают железо губчатое. Осн. массу Ж. выплавляют в виде сталей и чугунов Технически чистое Ж. применяют для изготовления сердечников электромагнитов, якорей электр. машин и др. Чистое Ж. используют как катализатор, для исследовательских целей и для изготовления медицинских препаратов. Порошки Ж., полученные восстановлением окислов, карбонильным и другими способами, перерабатывают методами порошковой металлургии в различные изделия, листы, полосы, ленты и др. Железный порошок в больших количествах используют при сварке, а также для цементации меди. Губчатое и кричное Ж. применяют для произ-ва высококачественных сталей. Ж. — составная часть железобетона и железографита. Окислы Ж. служат минеральными красками, а ферромагнитные Fe304 и v-Fe203 используют для произ-ва магнитных материалов. Из солей широко применяют сульфаты, напр. FeS04 X X 7Н20 — в текстильной пром-сти, в произ-ве берлинской лазури, чернил, минеральных красок , FeS04 — коагулянт для очистки во ды. Покрытие железом нашло применение в полиграфии — для изготовления клише, в автомобильной и тракторной промети — для восстановления изношенных деталей машин и др. На долю сплавов Ж. приходится примерно 95% всей металлической продукции.
Природная смесь состоит из четырёх стабильных изотопов железа : 54Fe ( 5,84% ) , 56Fe ( 91,68% ) ,57Fe (2,17%) , 58Fe (0,31% ) . Искусственные изотопы 55Fe и 59Fe применяется как радиоактивные индикаторы ( период полураспада 2,94 года и 45,1 дня ) .По распространённости на земле железо уступает среди металлов только алюминию . В литосфере его содержится 4,0% , в самородном состоянии встречается редко . Основные железные руды : магнитный железняк ( магнетит ) Fe3O4 , красный железняк ( гематит ) Fe2O3, бурый железняк ( лимонит ) 2Fe2O3 ⋅ 3h3O , шпатовый железняк ( сидерит ) FeCO3 . Железный колчедан ( пирит ) FeS2 перерабатывают на серную кислоту . Железо получают из руд путём восстановления , расплавленное железо растворяет избыток углерода и получается , сплав называемый чугун .
Химический процесс получения железа
Состоит :
При неполном сгорании кокса образуется оксид углерода ( II ) :
C + O2 = CO2↑
CO2 + C = 2CO↑
Оксид железа восстанавливается оксидом углерода ( II ) свободного железа :
3Fe2O3 + CO = 2Fe3O3 + CO2↑
Fe3O4 + CO = 3FeO + CO2↑
FeO + CO = Fe + CO2↑
Чугун содержит около 93% железа и 4% углерод , а также примеси кремния , марганца , фосфора и серы . Серый чугун содержит углерод в виде графита , а белый в виде цементита Fe3C . Из более мягкого и вязкого серого чугуна отливают чугунные изделия . Белый , трудно поддающийся обработке чугун перерабатывают на сталь , окисляя углерод кислородом воздуха в конвертерах , мартеновских или электропечах . Металл с содержанием углерода 0,3 — 2% называют твёрдой сталью . Мягкая сталь ( или железо ) содержит углерод менее 0,3% .
Такие стали приобретают твёрдость и вязкость , жаростойкость , кислотоупорность , противокоррозионные и другие ценные свойства . Среди них различают машиностроительные и инструментальные стали .
Поверхность стальных изделий иногда подвергают цементированию ( насыщение углеродом ) , азотированию ( нагревание в атмосфере аммиака ) , цианированию ( обогащение углеродом и азотом ) . В результате этого поверхность изделий приобретает твёрдость , устойчивость к истиранию и коррозии .
Чистое железо — серебристо — белый , мягкий металл , хорошо поддающийся обработке , легко намагничивается и размагничивается . Его получают электролизом растворов солей железа или термическим разложением пентакарбонила железа :
[Fe( CO )5 = Fe + 5CO↑
Известны четыре полиморфные модификации железа . Полиморфные превращения железа сопровождаются изменением кристаллической решётки и физических свойств железа .
При обычных температурах железо не взаимодействует даже с самыми активными неметаллами ( фтор , хлор , бром , йод , кислородом , серой , фосфором ) , но при нагревании реагирует с ними энергично . Во влажном воздухе техническое железо покрывается ржавчиной ( FeOOH ). Оно легко растворяется в соляной кислоте , в разбавленной серной и азотной кислотах , но концентрированные серная и азотная кислоты пассивирую железа . В щелочах ( кроме горячих концентрированных растворов ) оно нерастворимо .В устойчивых соединениях железо проявляет степени окисления +2 и +3 , имеет два простых оксида и один смешанный — оксид железа ( II , III ) Fe3O4 ( FeO ⋅ Fe2O3 ) .
Оксид железа ( II ) FeO — чёрный порошок . Он взаимодействует с кислотами , образуя соли железа ( II ) , проявляя основные свойства .
Гидроксид железа ( II ) Fe( OH )2 осаждают , действуя щелочами на растворы соли железа ( II ) :
FeSO4 + 2NaOH = Fe( OH )2↑ + Na2SO4
Гидроксид железа ( II ) амфотерен , частично растворяется в сильно щелочных средах . Это белое вещество легко окисляется кислородом воздуха до красно — бурого гидроксида железа ( III ) :
4Fe( OH )2 + O2 + 2h3O = 4Fe( OH )3
Гидроксид железа ( II ) легко растворяется в кислотах .
Оксид железа ( III ) Fe2O3 — красно — бурый порошок , обладает основными свойствами ( с признаками амфотерности ) , образует с кислотами соли железа ( III ) . Но при сплавлении с карбонатом натрия ( или щелочами ) Fe2O3 проявляет кислотные свойства и даёт соли метажелезистой кислоты HFeO2 — ферриты , например , феррит натрия NaFeO2 :
Fe2O3 + Na2CO3 = 2NaFeO2 + CO2↑
Гидроксид железа ( III ) Fe( OH )3 выпадает при действии щелочей на его железа ( III ) в виде красно — бурого осадка :
Fe2( SO4 )3 + 6NaOH = 2Fe( OH )3↓ + 3Na2SO4
Состав осадка не всегда отвечает своей формуле Fe( OH )3 считается , что железо ( III ) частично осаждается в виде HFeO3 . Гидроксид железа ( III ) проявляет основные свойства , растворятся в кислотах . Также он проявляет заметные свойства амфотерности с горячими концентрированными растворами щелочей . При растворении гидроксида железа ( III ) в щелочной среде получаются соли железной кислоты — ферраты K2FeO4 .
У железа хорошо выражена способность образовывать комплексные соединения . Прочным комплексный анион [Fe( CN )6] получается при взаимодействии солей железа ( II ) с цианидами :
FeSO4 + 6KCN = K4[Fe( CN )6] + K2SO4
Образующееся комплексное соединение — гексациано — ( II ) феррат калия ( жёлтая кровяная соль ) с солями железа ( III ) даёт интенсивно синий осадок берлинской лазури :
4FeCl3 + 3K4[Fe( CN )6] = Fe4[Fe( CN )6]3↓ + 12KCl
Гексациано — ( III ) феррат калия или красная кровяная соль , K3[Fe( CN )6] также выделяет из растворов солей железа ( II ) синий осадок :
3FeSO4 + 2K3[Fe( CN )6] = Fe3[Fe( CN )6]2↓ + 3K2SO4
которые раньше называли турнбуллевой синью .
Соли железа ( III ) с роданидами образуют кроваво — красные комплексы :
Fe³ᐩ + SCNˉ = [Fe( SCN )]²ᐩ
При высоких концентрации роданид — ионов получаются комплексные соединения с большим числом лигандов , например K3[Fe( SCN )6] .
Координационное число железа в комплексных соединениях равна шести .
Соли железа имеют практическое значение . Сульфат железа ( II ) или железный купорос , FeSO4 + 7h3O — сельскохозяйственный ядохимикат . Соль мора ( Nh5 )2SO4 ·FeSO4 · 6h3O или сульфат аммония — железа ( II ) , применяется в химическом анализе .
Велико биологическое значение железа , так как оно составная часть гемоглобина крови , в организме человека содержится около 3 граммов железа . Ионы железа участвуют а процессе переноса кислорода гемоглобином от лёгких к тканям и органам . Кроме того , железо содержится в печени и селезёнке человека и животных . Его недостаток вызывает заболевания . Железо необходим и растениям , оно участвует в окислительно — восстановительных процессах , в кислородном обмене . При недостатке железа в почве растения заболевают , замедляется синтез хлорофилла , задерживается их рост и развитие .
Лит.; Григорович В. К. Электронное строение и термодинамика сплавов железа Гиммельфарб А. И., Неменов А. М. Бескоксовая металлургия железа.
Железо — Мегаэнциклопедия Кирилла и Мефодия — статья
В периодической системе Менделеева железо входит в группу VIIIВ. В четвертом периоде, к которому принадлежит и железо, в эту группу входят также кобальт и никель. Эти три элемента образуют триаду и обладают сходными свойствами.Радиус нейтрального атома железа 0, 126 нм, радиус иона Fe2+ — 0, 080 нм, иона Fe3+ — 0, 067 нм. Энергии последовательной ионизации атома железа 7, 893, 16, 18, 30, 65, 57, 79 эВ. Сродство к электрону 0, 58 эв. По шкале Полинга электроотрицательность железа около 1, 8.
Железо высокой чистоты — это блестящий серебристо-серый, пластичный металл, хорошо поддающийся различным способам механической обработки.
В земной коре железо распространено достаточно широко — на его долю приходится около 4, 1% массы земной коры (4-е место среди всех элементов, 2-е среди металлов). Известно большое число руд и минералов, содержащих железо. Наибольшее практическое значение имеют красные железняки (руда гематит, Fe2O3; содержит до 70% Fe), магнитные железняки (руда магнетит, Fe3О4; содержит 72, 4% Fe), бурые железняки (руда гидрогетит НFeO2·nH2O), а также шпатовые железняки (руда сидерит, карбонат железа, FeСО3; содержит около 48% Fe). В природе встречаются также большие месторождения пирита FeS2 (другие названия — серный колчедан, железный колчедан, дисульфид железа и другие), но руды с высоким содержанием серы пока практического значения не имеют. По запасам железных руд Россия занимает первое место в мире. В морской воде 1·10-5—1·10-8% железа.Железо играло и играет исключительную роль в материальной истории человечества. Первое металлическое железо, попавшее в руки человека, имело, вероятно, метеоритное происхождение. Руды железа широко распространены и часто встречаются даже на поверхности Земли, но самородное железо на поверхности крайне редко. Вероятно, еще несколько тысяч лет назад человек заметил, что после горения костра в некоторых случаях наблюдается образование железа из тех кусков руды, которые случайно оказались в костре. При горении костра восстановление железа из руды происходит за счет реакции руды как непосредственно с углем, так и с образующимся при горении оксидом углерода (II) СО. Возможность получения железа из руд существенно облегчило обнаружение того факта, что при нагревании руды с углем возникает металл, который далее можно дополнительно очистить при ковке. Получение железа из руды с помощью сыродутного процесса было изобретено в Западной Азии во 2-м тыс. до н. э. Период с 9 по 7 в. до н. э., когда у многих племен Европы и Азии развилась металлургия железа, получил название железного века, пришедшего на смену бронзовому веку. Усовершенствование способов дутья (естественную тягу сменили меха) и увеличение высоты горна (появились низкошахтные печи — домницы) привело к получению чугуна, который стали широко выплавлять в Западной Европе с 14 века. Полученный чугун переделывали в сталь. С середины 18 века в доменном процессе вместо древесного угля начали использовать каменно-угольный кокс. В дальнейшем способы получения железа из руд были значительно усовершенствованы, и в настоящее время для этого используют специальные устройства — домны, кислородные конвертеры, электродуговые печи.При температурах от комнатной и до 917 °C, а также в интервале температур 1394-1535 °C существует α-Fe с кубической объемно центрированной решеткой, при комнатной температуре параметр решетки а = 0, 286645 нм. При температурах 917-1394 °C устойчиво β-Fe с кубической гранецентрированной решеткой Т (а = 0, 36468 нм). При температурах от комнатной до 769 °C (так называемая точка Кюри) железо обладает сильными магнитными свойствами (оно, как говорят, ферромагнитно), при более высоких температурах железо ведет себя как парамагнетик. Иногда парамагнитное α-Fe с кубической объемно центрированной решеткой, устойчивое при температурах от 769 до 917 °C, рассматривают как γ-модификацию железа, а β-Fe, устойчивое при высоких температурах (1394-1535 °C), называют по традиции δ-Fe (представления о существовании четырех модификаций железа — α, β, γи δ— возникли тогда, когда еще не существовал рентгеноструктурный анализ и не было объективной информации о внутреннем строении железа). Температура плавления 1535 °C, температура кипения 2750 °C, плотность 7, 87 г/см3. Стандартный потенциал пары Fe2+/Fe0 –0, 447В, пары Fe3+/Fe2+ +0, 771В.При хранении на воздухе при температуре до 200 °C железо постепенно покрывается плотной пленкой оксида, препятствующего дальнейшему окислению металла. Во влажном воздухе железо покрывается рыхлым слоем ржавчины, который не препятствует доступу кислорода и влаги к металлу и его разрушению. Ржавчина не имеет постоянного химического состава, приближенно ее химическую формулу можно записать как Fe2О3·хН2О.
С кислородом железо реагирует при нагревании. При сгорании железа на воздухе образуется оксид Fe2О3, при сгорании в чистом кислороде — оксид Fe3О4. Если кислород или воздух пропускать через расплавленное железо, то образуется оксид FeО. При нагревании порошка серы и железа образуется сульфид, приближенную формулу которого можно записать как FeS.
Железо при нагревании реагирует с галогенами. Так как FeF3 нелетуч, железо устойчиво к действию фтора до температуры 200-300°C. При хлорировании железа (при температуре около 200°C) образуется летучий FeСl3. Если взаимодействие железа и брома протекает при комнатной температуре или при нагревании и повышенном давлении паров брома, то образуется FeBr3. При нагревании FeСl3 и, особенно, FeBr3 отщепляют галоген и превращаются в галогениды железа (II). При взаимодействии железа и иода образуется иодид Fe3I8.При нагревании железо реагирует с азотом, образуя нитрид железа Fe3N, с фосфором, образуя фосфиды FeP, Fe2P и Fe3P, с углеродом, образуя карбид Fe3C, с кремнием, образуя несколько силицидов, например, FeSi.
При повышенном давлении металлическое железо реагирует с монооксидом углерода СО, причем образуется жидкий, при обычных условиях легко летучий пентакарбонил железа Fe(CO)5. Известны также карбонилы железа составов Fe2(CO)9 и Fe3(CO)12. Карбонилы железа служат исходными веществами при синтезе железоорганических соединений, в том числе и ферроцена состава [Fe(-C5H5)2].Чистое металлическое железо устойчиво в воде и в разбавленных растворах щелочей. В концентрированной серной и азотной кислотах железо не растворяется, так как прочная оксидная пленка пассивирует его поверхность.
С соляной и разбавленной (приблизительно 20%-й) серной кислотами железо реагирует с образованием солей железа (II):
Fe + 2HCl = FeCl2 + H2
Fe + H2SO4 = FeSO4 + H2
При взаимодействии железа с приблизительно 70%-й серной кислотой реакция протекает с образованием сульфата железа (III):
2Fe + 4H2SO4 = Fe2(SO4)3 + SO2 + 4H2O
Оксид железа (II) FeО обладает основными свойствами, ему отвечает основание Fe(ОН)2. Оксид железа (III) Fe2O3 слабо амфотерен, ему отвечает еще более слабое, чем Fe(ОН)2, основание Fe(ОН)3, которое реагирует с кислотами:
2Fe(ОН)3 + 3H2SO4 = Fe2(SO4)3 + 6H2O
Гидроксид железа (III) Fe(ОН)3 проявляет слабо амфотерные свойства; он способен реагировать только с концентрированными растворами щелочей:
Fe(ОН)3 + КОН = К[Fe(ОН)4]
Образующиеся при этом гидроксокомплексы железа (III) устойчивы в сильно щелочных растворах. При разбавлении растворов водой они разрушаются, причем в осадок выпадает гидроксид железа (III) Fe(OH)3.
Соединения железа (III) в растворах восстанавливаются металлическим железом:
Fe + 2FeCl3 = 3FeCl2
При хранении водных растворов солей железа (II) наблюдается окисление железа (II) до железа (III):
4FeCl2 + O2 + 2H2O = 4Fe(OH)Cl2Из солей железа (II) в водных растворах устойчива соль Мора — двойной сульфат аммония и железа (II) (NH4)2Fe(SO4)2·6Н2О.
Железо (III) способно образовывать двойные сульфаты с однозарядными катионами типа квасцов, например, KFe(SO4)2 — железокалиевые квасцы, (NH4)Fe(SO4)2 — железоаммонийные квасцы и т. д.
При действии газообразного хлора или озона на щелочные растворы соединений железа (III) образуются соединения железа (VI) — ферраты, например, феррат (VI) калия K2FeO4. Имеются сообщения о получении под действием сильных окислителей соединений железа (VIII).
Для обнаружения в растворе соединений железа (III) используют качественную реакцию ионов Fe3+ с тиоцианат-ионами CNS—. При взаимодействии ионов Fe3+ с анионами CNS— образуется ярко-красный роданид железа Fe(CNS)3. Другим реактивом на ионы Fe3+ служит гексацианоферрат (II) калия K4[Fe(CN)6] (ранее это вещество называли желтой кровяной солью). При взаимодействии ионов Fe3+ и [Fe(CN)6]4- выпадает ярко-синий осадок.
Реактивом на ионы Fe2+ в растворе может служить раствор гексацианоферрат (III) калия K3[Fe(CN)6], ранее называвшийся красной кровяной солью. При взаимодействии ионов Fe3+ и [Fe(CN)6]3- выпадает ярко-синий осадок такого же состава, как и в случае взаимодействия ионов Fe3+ и [Fe(CN)6]4-.
Железо используется главным образом в сплавах, прежде всего в сплавах с углеродом — различных чугунах и сталях. В чугуне содержание углерода выше 2, 14 % по массе (обычно — на уровне 3, 5-4%), в сталях содержание углерода более низкое (обычно на уровне 0, 8-1 %).
Чугун получают в домнах. Домна представляет собой гигантский (высотой до 30-40 м) усеченный конус, полый внутри. Стенки домны изнутри выложены огнеупорным кирпичом, толщина кладки составляет несколько метров. Сверху в домну вагонетками загружают обогащенную (освобожденную от пустой породы) железную руду, восстановитель кокс (каменный уголь специальных сортов, подвергнутый коксованию — нагреванию при температуре около 1000 °C без доступа воздуха), а также плавильные материалы (известняк и другие), способствующие отделению от выплавляемого металла примесей — шлака. Снизу в домну подают дутье (чистый кислород или воздух, обогащенный кислородом). По мере того, как загруженные в домну материалы опускаются, их температура поднимается до 1200-1300 °C. В результате реакций восстановления, протекающих главным образом с участием кокса С и СО:
Fe2O3 + 3C = 2Fe + 3CO;
Fe2O3 + 3CО = 2Fe + 3CO2
возникает металлическое железо, которое насыщается углеродом и стекает вниз.
Этот расплав периодически выпускают из домны через специальное отверстие — летку — и дают расплаву застыть в специальных формах. Чугун бывает белый, так называемый передельный (его используют для получения стали) и серый, или литьевой. Белый чугун — это твердый раствор углерода в железе. В микроструктуре серого чугуна можно различить микрокристаллики графита. Из-за наличия графита серый чугун оставляет след на белой бумаге.
Чугун хрупок, при ударе он колется, поэтому из него нельзя изготавливать пружины, рессоры, любые изделия, которые должны работать на изгиб.
Твердый чугун легче расплавленного, так что при его затвердевании происходит не сжатие (как обычно при затвердевании металлов и сплавов), а расширение. Эта особенность позволяет изготавливать из чугуна различные отливки, в том числе использовать его как материал для художественного литья.
Если содержание углерода в чугуне снизить до 1, 0-1, 5%, то образуется сталь. Стали бывают углеродистыми (в таких сталях нет других компонентов, кроме Fe и C) и легированными (такие стали содержат добавки хрома, никеля, молибдена, кобальта и других металлов, улучшающие механические и иные свойства стали).
Стали получают, перерабатывая чугун и металлический лом в кислородном конвертере, в электродуговой или мартеновской печах. При такой переработке снижается содержание углерода в сплаве до требуемого уровня, как говорят, избыточный углерод выгорает.
Физические свойства стали существенно отличаются от свойств чугуна: сталь упруга, ее можно ковать, прокатывать. Так как сталь, в отличие от чугуна, при затвердевании сжимается, то полученные стальные отливки подвергают обжатию на прокатных станах. После прокатки в объеме металла исчезают пустоты и раковины, появившиеся при затвердевании расплавов.
Производство сталей имеет в России давние глубокие традиции, и полученные нашими металлургами стали отличаются высоким качеством.
Чистое железо имеет довольно ограниченное применение. Его используют при изготовлении сердечников электромагнитов, как катализатор химических процессов, для некоторых других целей. Но сплавы железа — чугун и сталь — составляют основу современной техники. Находят широкое применение и многие соединения железа. Так, сульфат железа (III) используют при водоподготовке, оксиды и цианид железа служат пигментами при изготовлении красителей и так далее.
Железо присутствует в организмах всех растений и животных как микроэлемент, то есть в очень малых количествах (в среднем около 0, 02%). Однако железобактерии, использующие энергию окисления железа (II) в железо (III) для хемосинтеза, могут накапливать в своих клетках до 17-20% железа. Основная биологическая функция железа — участие в транспорте кислорода и окислительных процессах. Эту функцию железо выполняет в составе сложных белков — гемопротеидов, простетической группой которых является железопорфириновый комплекс — гем. Среди важнейших гемопротеидов дыхательные пигменты гемоглобин и миоглобин, универсальные переносчики электронов в реакциях клеточного дыхания, окисления и фотосинеза цитохромы, ферменты каталоза и пероксида, и других. У некоторых беспозвоночных железосодержащие дыхательные пигменты гелоэритрин и хлорокруорин имеют отличное от гемоглобинов строение. При биосинтезе гемопротеидов железо переходит к ним от белка ферритина, осуществляющего запасание и транспорт железа. Этот белок, одна молекула которого включает около 4 500 атомов железа, концентрируется в печени, селезенке, костном мозге и слизистой кишечника млекопитающих и человека. Суточная потребность человека в железе (6-20 мг) с избытком покрывается пищей (железом богаты мясо, печень, яйца, хлеб, шпинат, свекла и другие). В организме среднего человека (масса тела 70 кг) содержится 4, 2 г железа, в 1 л крови — около 450 мг. При недостатке железа в организме развивается железистая анемия, которую лечат с помощью препаратов, содержащих железо. Препараты железа применяются и как общеукрепляющие средства. Избыточная доза железа (200 мг и выше) может оказывать токсичное действие. Железо также необходимо для нормального развития растений, поэтому существуют микроудобрения на основе препаратов железа.- Конецкая Д. С. и др. Железо высокой степени чистоты. М., 1978.
- Путешествие в страну элементов: Сборник. М.: Молодая гвардия. 1963.
- Каменецкая Д. С., Пилецкая И. Б., Ширяев В. И. Железо высокой степени чистоты. М., 1978.
- Пикеринг Ф. Физическое металловедение и разработка сталей. М., 1982.
Добавить комментарий